3 Benefits Of A Manufacturing Safety Checklist (And Where To Get One)

Workplace safety has always been a priority in the heavy manufacturing industry. But, sometimes, it’s hard to see the progress.
In 2019, the total cost of safety incidents at work was $171 billion. That comes out to about $1,100 per employee per year. And, similar to previous years, the manufacturing industry ranks third for on-the-job incidents, with an average of 400,000 non-fatal injuries a year.
As manufacturers bounce back from the 2020 global health crisis, business leaders are looking to do more to create safe and healthy workplaces.
With a heavy manufacturing checklist in hand, companies are better prepared to:
- Optimize their operations
- Safeguard their busy workplace environments
- Reduce factory floor risks for the most exposed workers
- Build a culture of safety within their business
Curious about the benefits of having a heavy manufacturing safety checklist? Check out our top three below!
1. Quickly and Easily Share Workplace Protocols

In frontline-first industries, like manufacturing, businesses are still playing catch-up in adopting workplace collaboration technologies that reach their most essential employees. But, that is changing quickly as the COVID-19 pandemic has dramatically accelerated the process of digitization for these industries.
In 2021, employee health and safety continue to be the focal point of workplace conversations – regardless of if they’re in the break room or the board room.
With a safety checklist, heavy manufacturers have what they need to develop a strategy for sharing important safety information to all employees.
Some of their steps may include:
- Providing regular workplace safety training and education
- Adopting a mobile productivity tool to reach frontliners no matter where they are
- Communicating with employees in their native language
2. Build A Safety-First Company Culture
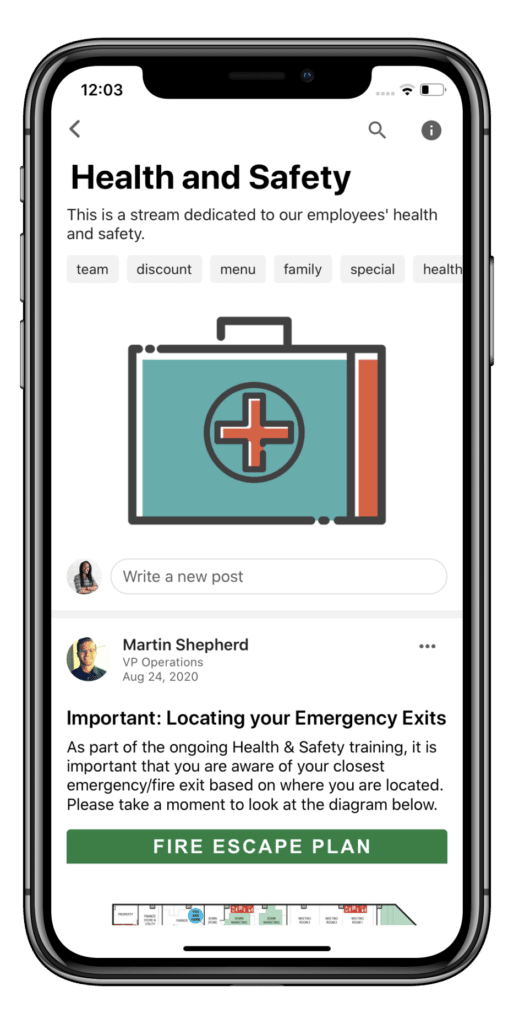
Businesses that succeed in creating safe work environments are the ones that empower their employees to champion safety protocols. That usually calls for a highly engaged workforce that wants to see their businesses operate to the highest safety standards possible.
By starting with a safety checklist, heavy manufacturers are building a company culture that prioritizes workplace safety. Some ways companies are fostering a culture of safety include:
- Establishing a workplace safety committee with representatives from all levels – including the front line
- Implementing company-wide safety campaigns
- Requesting transparent feedback from frontline workers
3. Decrease Annual Safety-Related Costs
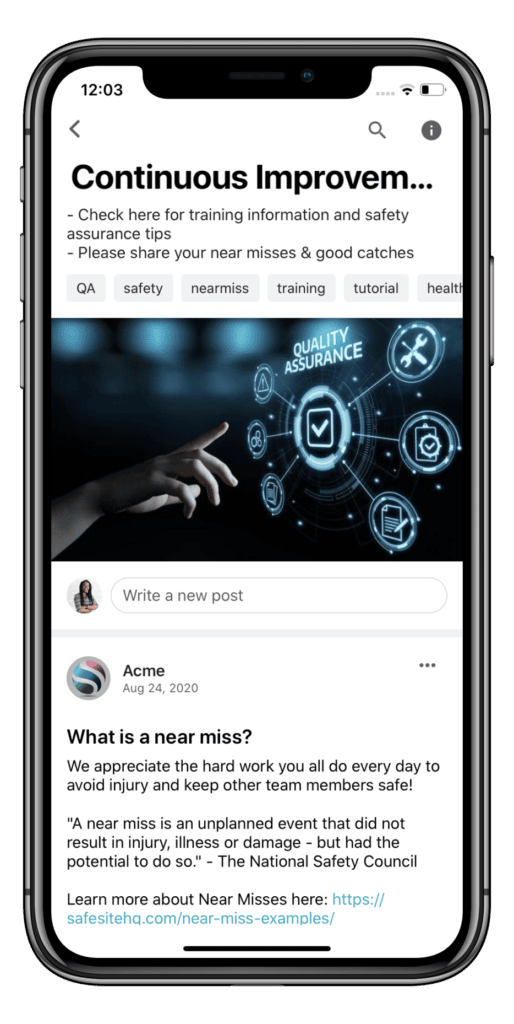
The expense of poor workplace safety protocols is costly. But have no fear! Businesses can address these creeping costs with a safety checklist and better employee engagement.
A recent Gallup research study found that highly engaged organizations experience 70% fewer safety incidents at work.
Mobile collaboration and productivity platforms are one way heavy manufacturers are ramping up frontline employee engagement. With a mobile communication solution, a company can save an estimated $770,000 per 1,000 employees by:
- Ensuring frontline employees are up-to-date on all critical company information
- Providing instant access to necessary safety information directly on workers’ mobile devices
- Sharing safety best practices across the entire organization
- Recognizing employees that go above and beyond to maintain a safety-first workplace culture
Download our manufacturing safety checklist here!

About the author
Beekeeper
Interested in learning more?
Join 1200+ companies transforming frontline work with Beekeeper. Start your journey today to make every task easier, every team stronger, and every shift smoother.