Reducing Manufacturing Overhead: 3 Key Ways
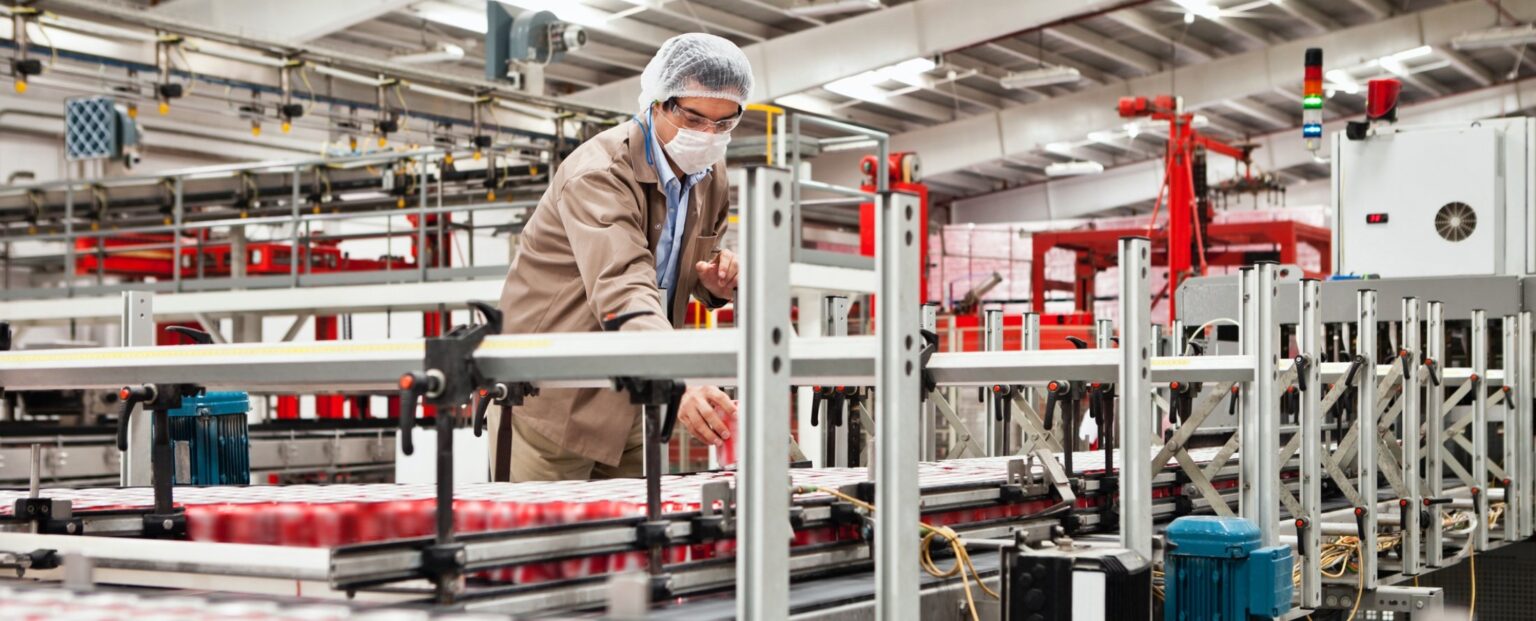
For manufacturing companies, recovering from the pandemic and adjusting to a new normal involves making strategic decisions about how best to allocate resources. Manufacturing overhead is often the first place where companies look when wanting to cut costs, as it doesn’t directly support the production process.
While calculating manufacturing overhead costs is relatively simple, knowing which costs to prioritize can be more tricky. One of the more overlooked categories in manufacturing overhead is the set of communications tools a company uses to connect their workforce.
The right communication tools can not only reduce manufacturing overhead but uncover areas where companies can further cut costs.
We’ll go more into depth about what manufacturing means, how to calculate manufacturing overhead, and why reducing overhead costs can increase operational efficiency.
What Is Manufacturing Overhead?
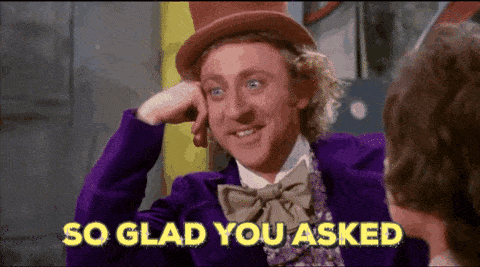
Manufacturing costs take into account all of the resources that go into making a product. They’re usually separated into the direct cost of materials, direct cost of labor, and manufacturing overhead.
Manufacturing overhead includes all of the indirect costs accumulated during the production process during a specific period of time.
Here are some manufacturing overhead examples:
- Rent of a factory building
- Cost of utilities used to keep the production space running
- Salaries of workers other than those directly involved in production, like janitors or plant managers
- Internet and communication services costs
- Depreciation on equipment
- Property taxes on manufacturing space
- Repair costs
- Insurance
Manufacturing overhead strictly refers to the indirect costs of the production process. It does not include administrative costs like corporate salaries, legal fees, and marketing expenses.
How to Find Manufacturing Overhead
To calculate manufacturing overhead, identify the essential costs that keep the production process running. Costs like rent and utilities fall into this category.
Then add the costs that keep the production process running smoothly. That could include expenses to increase company morale, like team lunches. Or, it could include software and communication platforms that keep teams connected and informed.
Calculating the total manufacturing overhead cost is pretty straightforward. You take the sum of all indirect costs incurred during a production period. You can then further divide that cost by the number of units produced to find out how much overhead is spent per unit.
Now let’s look at how identifying each indirect cost can help companies manage their manufacturing overhead budget better.
How Can Calculating Your Manufacturing Overhead Reduce Costs?
Manufacturing overhead is an ongoing expense, regardless of whether or not a company is making any money. The production process may slow down, but some overhead costs are inevitable.
As the manufacturing industry had to adapt to social distancing guidelines and shifting economic demand, companies have had to take a hard look at reducing their manufacturing overhead costs.
In many cases, reducing staff to all but the essential employees meant that companies could cut down on overhead costs like electricity bills. At the same time, they’ve had to allocate part of their manufacturing overhead budget to health and safety measures, like keeping factory floors sanitary and providing staff with PPE.
The Role of Internal Communication in Manufacturing Overhead
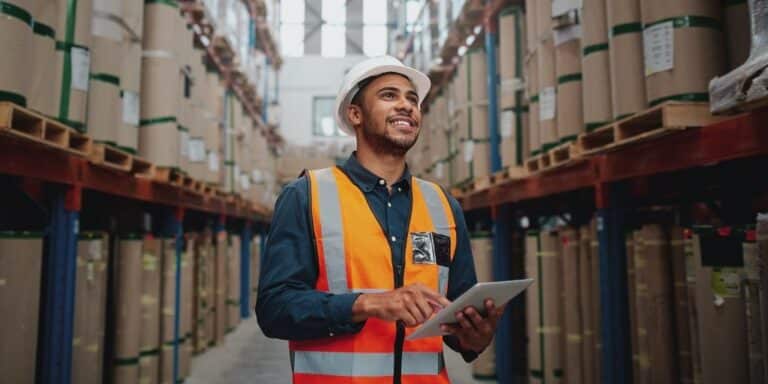
Remember how we said that manufacturing overhead costs include those that keep the production process running smoothly?
One of the most important, yet overlooked, overhead costs is the role of mobile communication in manufacturing. When companies are able to integrate digital technology effectively, they can reduce unnecessary overhead costs and boost production efficiency.
Manufacturing companies may overlook the importance of digital communication tools for their employees because factory work is so hands-on. Unlike office workers, frontline employees in manufacturing aren’t typically checking their computers all day and may not even have a company email address.
But adopting the right digital tools for manufacturing employees can dramatically improve communication on the production floor. That, in turn, can make it easier to reduce overhead costs.
Here are three key ways that mobile communication can reduce manufacturing overhead.
1) Better Shift Scheduling
Reducing manufacturing overhead involves scheduling shifts in a way that makes use of space and resources in the most efficient manner possible.
During the pandemic, that means scheduling shifts that minimize the number of employees working at one time while maximizing output. But even after the pandemic is no longer a concern, efficient shift scheduling is one way to reduce overhead costs.
Digital tools allow managers to assign and change shifts knowing that workers will see and acknowledge those changes in real-time. And when the salaries of factory managers are often considered an overhead cost, tools that allow for quicker scheduling will further reduce manufacturing overhead.
2) Improved Training and Onboarding
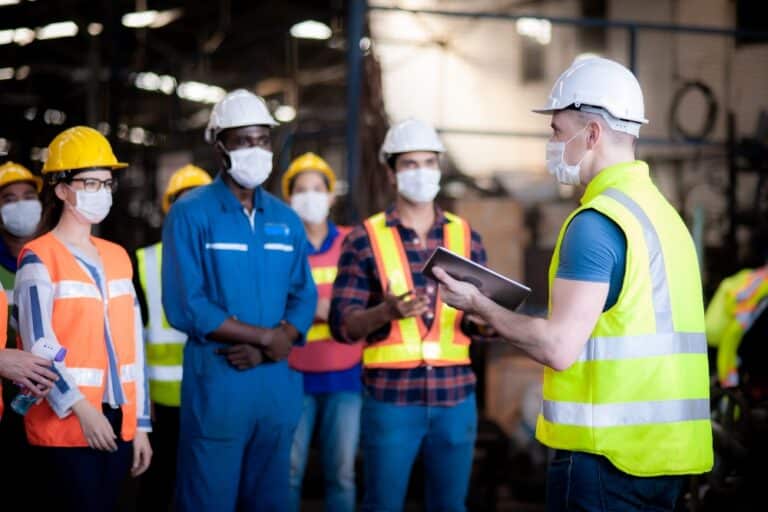
Here’s what can fall into the category of indirect training costs:
- Compensation during the training process
- Cost of the time required to set up training
- Administrative costs related to training
- Utilities costs during training process
That can add up to a lot of overhead costs before an employee is even ready to start working.
The Institute for Research on Labor and Employment found that onboarding can take more than 65 hours and two months for employees to be fully productive.
Mobile training tools that don’t require new employees to be on-site can reduce or eliminate the utilities costs of training. And when the onboarding process is easily accessible on mobile, companies can let the tool do much of the work to save on administrative costs.
3) Gathering Workforce Feedback
Reducing manufacturing overhead isn’t just about the leadership team making executive decisions about where to cut costs.
Frontline production employees working on the shop floor every day are a rich source of information on specific ways the company can maximize its resources.
With an internal communication strategy that prioritizes frontline feedback loops, companies can collaborate and prioritize ways to reduce overhead.
Using an employee communication app like Beekeeper, for example, allows managers to set up surveys that ask employees if any resources are being wasted. Companies can then take that feedback into consideration and make more informed decisions about their manufacturing overhead budget.
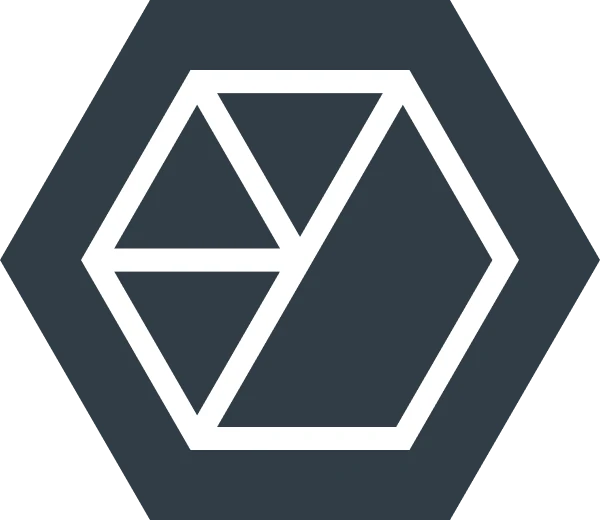
About the author
Beekeeper
We make frontline lives easier, work safer, and teams more connected so businesses can reach new heights. At Beekeeper, we’re dedicated to making frontline lives easier by connecting workers with the tools, support, and information they need to feel valued, do their best work, and drive the business forward.