Lean Operations and How You Can Use It to Save Money
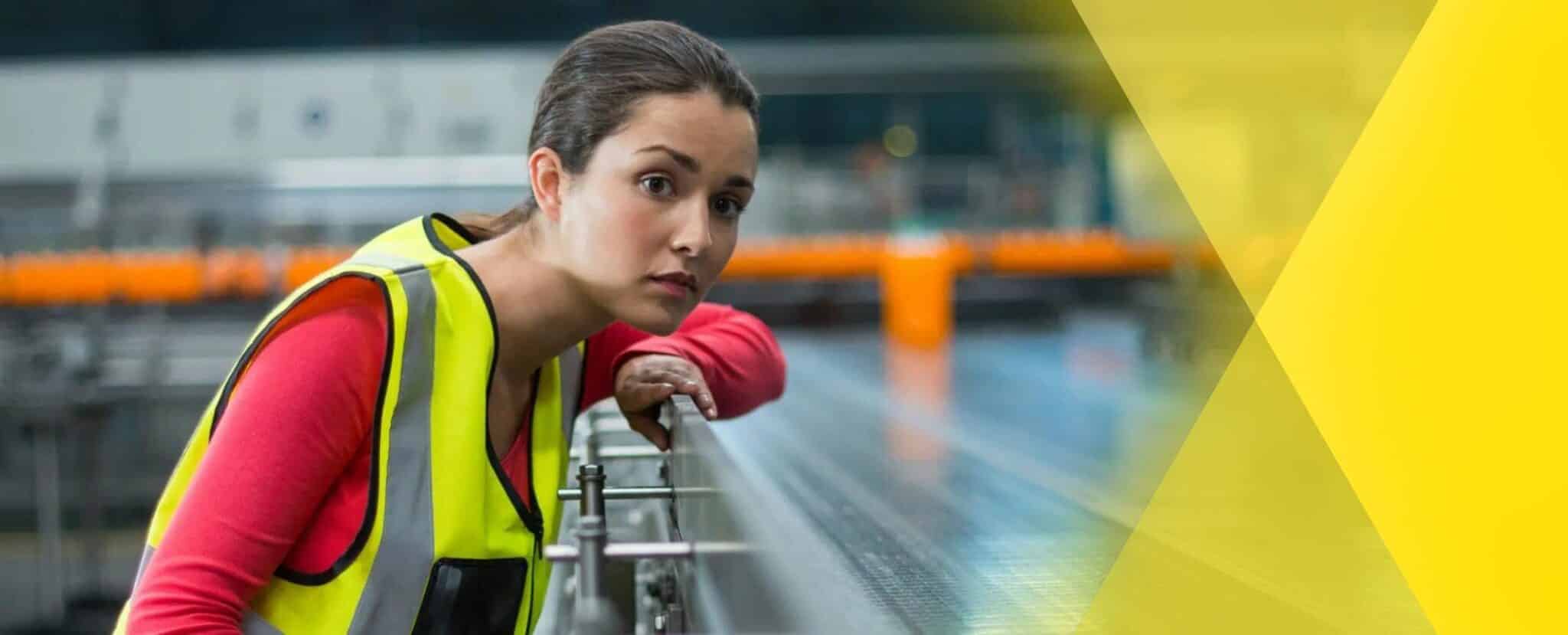
Table of contents
- What Is Lean Operations?
- Why Is Lean Operations Important?
- Which Industries Can Benefit From Lean Operations Management?
- Two Lean Management Operations Examples
- How Lean Operations Management Empowers Workers
- 5 Best Practices For a Lean Operations Strategy
- Lean Operations for Better Business Outcomes
- Most Frequently Asked Questions
No matter what type of business you run, cutting costs and operating more efficiently should be a top priority. It’s called lean operations, and it’s a key strategy for improving internal functions, creating a productive and engaged workforce, and increasing profits.
As companies face increasing competition at home and abroad, finding better, faster, less expensive ways to operate is necessary to remain relevant and stay in business. The concept of lean management is a method companies have been using for almost a century. The ROI of lean operations promises greater employee engagement and a bigger bottom line.
What Is Lean Operations?
Lean operations is a business strategy driven by the principle of doing more with less. It is a minimalist approach to running a business and improving day-to-day operations.
In other words, lean operations is all about putting a little Marie Kondo-like efficiency into your workflows.
According to the Lean Enterprise Institute,
“A lean organization understands customer value and focuses its key processes to continuously increase it. The ultimate goal is to provide perfect value to the customer through a perfect value creation process that has zero waste.”
There are lean operations examples in every industry though it is often associated with lean manufacturing. Amazon.com is one company that exemplifies this approach with a commitment to the customer that defines its internal operations strategy. After 25 years, they still follow their original mission: “We aim to be Earth’s most customer-centric company.”
How? Through the continuous improvement strategy that is the foundation of lean operations—“innovating new solutions to make things easier, faster, better, and more cost-effective.” Their goal to get products to customers at an unrivaled pace requires every step in the supply chain to be as efficient as possible.
Putting lean operation principles into practice begins with an in-depth analysis of your organization’s processes and finding alternative, more efficient ways to achieve your business goals. It also includes optimizing the tangible elements of a business, such as the workforce and physical environment, to improve overall output and performance.
The ultimate goal of creating a lean environment is to cut costs and eliminate wasted energy, resources, and time, and improve operational excellence. This is usually achieved through building a deliberate workforce structure, an optimized facility, and refined processes. Lean operations management is often supported by digital transformations that streamline communication and automate internal tasks.
Why Is Lean Operations Important?
Running a business as efficiently as possible may seem like an obvious goal, but even the more prolific business leaders can easily get bogged down in the day-to-day operations. It’s easy to forget to take a step back and take stock of the organization on a more holistic level.
Without a deep dive into an organization’s supply chain, companies often fall into one of five operational “traps” that can be difficult to overcome:
- Overproduce items through an inefficient production process
- Hold onto too much inventory
- Incur cost overages
- Experience unproductive downtime
- Have employees duplicate tasks
By improving internal processes, a company is better positioned to uncover hidden operational costs and offer value to its customers through its products or services.
Optimizing internal functions through a lean management system has a number of business benefits:
- Improves workflow efficiency
- Creates an agile workforce able to pivot and adapt to new models of operating
- Eliminate waste
- Reduces operating expenditures and yields greater profits
- Enables long-term operational viability
- Facilitates more sustainable solutions
- Boosts value proposition
In today’s world, building a high-functioning company is more important than ever. Taking a lean approach to operations management creates business agility—a necessary attribute to prepare for and survive a crisis.
But a crisis can also be the perfect catalyst to adopt lean management principles. A turbulent event can reveal weak spots in your workflows and create the perfect opportunity to chart a new course.
With a lean management strategy, companies can withstand sudden changes and limit disruptions so they can continue to produce value for their stakeholders.
Which Industries Can Benefit From Lean Operations Management?
The lean operations definition is consistent across industries, but the way a business incorporates a lean operations strategy is specific to the needs of a company. Almost any company can benefit from a shorter lead time.
Any company that makes and/or distributes goods or provides a service to customers can benefit from this approach.
Some industries that are particularly well-suited for lean management operations include:
Retail
Retail operations revolve around the numbers—inventory amount, and total sales. At Wireless Vision, the operator of more than 650 T-mobile stores, they host many of their internal files and procedures on Beekeeper’s mobile platform.
This single-entry point allows all 4,000 employees to connect in one place for easy exchange of information. Using confirmation campaigns, employees can send and receive information in seconds which is essential for sales associates on the floor working with customers. Efficient communication is essential for boosting sales.
Manufacturing
The term, “Lean operations” is well-known within the manufacturing space — the concept of “lean” originated in the auto industry in an effort to improve the production process. Manufacturing has gone through several major transformations (think Industrial Revolution), and companies often reflect on what is lean operations management in order to speed up lead times at lower costs.
As manufacturing evolves and technology allows smoother operations, there are many lean manufacturing examples of companies that are reducing waste, working more efficiently, and saving money. There are also opportunities for manufacturing training programs to give staff the skills they need to operate in a lean environment.
Lean operations management can eliminate waste by up to 35%. Holcim, a global producer of building materials, used a digital solution for communication and connected 1,500 mobile employees in one place. As a result, this lean manufacturing strategy saved $50,000 by eliminating the cost of printing their newsletter.
Hospitality
With the rise of the sharing economy, hospitality companies have had to find new ways to stay competitive. With a lean mindset and processes in place, hospitality companies can strengthen brand reputation, lower turnover, and improve customer service.
At 1 Hotels, a luxury brand with several properties around the US, a mobile communication tool created continuity between shift workers. Real-time communication improved their guest stays and managers migrated tasks, like employee onboarding, to the digital platform to streamline processes and save time
Two Lean Management Operations Examples
Henry Ford first coined the phrase “flow production.” He was a pioneer in linear production, creating steps that followed a sequence that came to be known as the assembly line. Since then, companies have adopted that strategy to achieve higher quality production with a simpler, more efficient lean operating system.
Toyota
The Japanese automobile manufacturer might be the most famous lean manufacturing operations case study out there, driven by the principle of kaizen—a belief in continuous improvement. Since the company was founded, leadership has sought ways to constantly evolve and better workflows that result in a quality vehicle. They called it the Toyota Production System.
Toyota’s workflows do not expend excess energy or use materials unnecessarily. Instead, driven by the “Just in Time” method, production lines make only what they need, as they need it, allowing workers to focus on one car at a time.
Toyota has become so well known for its TPS approach that it created the Toyota Production System Support Center, a non-profit that helps small businesses benefit from the same lean principles they operate by.
Nike
While Nike’s brand recognition is unparalleled in the athletic shoe world, its quest to deliver a great product hinges on its dedication to creating value through continuous improvement of its internal structure and processes.
Nike achieves lean operations through specific goal-setting that aligns its entire enterprise to its mission and products. From supply chain management to HR processes, Nike regularly audits its various internal components. As a result, Nike has decreased CO2 emissions by 6% while increasing output by 20%. Through lean operations, Nike has created long-term marketplace stability and decreased product defects by 50%.
How Lean Operations Management Empowers Workers
Lean operations are more than just a functional approach to business. Lean must be a core value of a company’s culture because operations management intersects directly with the employee experience.
Let’s look at Amazon again. Though they implement new technology and automate repetitive processes to keep things moving, their workforce is a major focus of their lean management strategy. “Part of lean is the strong engagement of the front line,” Marc Onetto told McKinsey. As Amazon’s former head of global operations, he knows firsthand the importance of the frontline. “Amazon has more people working in the fulfillment centers and customer-service centers than it does computer-science engineers. We needed the engagement of all these people to succeed,” said Onetto.
The first question you might hear from your workforce is, “What are lean operations?” Be transparent with employees on what a lean approach means to the company and how the change will also benefit them.
Lean manufacturing is a great opportunity to empower and engage your workforce through a well-defined purpose.
Here’s how:
- Include an organizational flow that ensures that every position is essential to the overall process. This brings deeper meaning to every role and enables employees to understand their value
- Lean production in operations management creates opportunities for professional development. For instance, as technology automates and improves processes, leaders can upskill employees for new positions within the company
- Ask employees for feedback that can help map out a lean transformation strategy that will deepen engagement. For instance, asking frontline workers for their insight into what operational elements are slow and weak from their perspective will help guide lean decision-making
- Create opportunities for employees to be change management leaders within their departments
- Enhance the employee journey with a frontline success system that will support lean transformation
Engaging employees supports the overall goal of lean operations management—to boost productivity and reduce wasted time through greater retention and less absenteeism.
5 Best Practices For a Lean Operations Strategy
Here are five best practices to begin your transformation to become a lean organization and maximize performance.
1. Assess your organization
Before you can make changes, you need to evaluate your organization—your workflows and processes, the structure of your workforce, your inventory, and your physical workspace. Next, revisit your company’s mission statement and goals. Are you achieving them in the most efficient way?
Learn where the most time, energy, and money get wasted. Do you have too much inventory? Do you tend to run behind schedule? Determine what elements are repetitive or unnecessary to achieving your company’s goals. Look at your company from different angles to discover new ways of doing things.
2. Implement new processes
Now, rethink your organizational processes. Map out your value stream from end to end using alternative strategies that are more time and cost-efficient than how they are now. If you have more than one idea, experiment to see which alternative method works best. Introduce technology that can improve internal workflows and each production process.
Find software that can help your organization lighten the load and improve workflows by breaking down silos and integrating systems. Find suppliers who also follow a lean operations model to ensure you source raw materials that will contribute to your product’s value.
3. Streamline communications
To truly have a lean operations management approach, communication needs to be direct and enterprise-wide. Use a frontline success system to connect everyone in your company that allows them to communicate in real-time.
71% of frontline workers say digital communication makes them more productive.
It allows fast collaboration for quick problem solving, eliminating those lingering issues that are a costly thorn in the side. Workplace tech also gathers actionable data and creates a silo-free organization that integrates data systems to create one hub for all communication. For instance, you can create a document library where employees can easily find job-related information when they need it.
4. Restructure your workforce and include them in lean transformation
As part of evaluating your organization, you’ll need to examine every role in your workforce. Where are employees doubled up on tasks? Are you tapping into every worker’s potential value to your company?
Upskill your workforce to fill the new jobs you’ll need in a lean environment, which will empower employees while also ensuring every role has a unique contribution to the value stream.
5. Embrace automation
A lot of company waste happens due to human error. From administrative functions to production lines, many tasks can now be automated to avoid costly errors and workflow disruptions. For example, when a manufacturer automates production lines they experience faster output and a safer work environment.
Reassigning repetitive tasks to smart machines also saves money on unnecessary downtime. They can also communicate when they need maintenance, reducing unplanned downtime from broken systems which can sometimes cost companies $260,000 an hour.
Lean Operations for Better Business Outcomes
Running a lean organization goes beyond a one-time transformation. It is an ongoing process in which a company continually evaluates how they can improve their workflows. Always keep your eye out for new ways of doing things that can make your company run better, empower and engage your workforce, and deliver higher returns.
Most Frequently Asked Questions
What do you mean by lean operations?
“A lean organization understands customer value and focuses its key processes to continuously increase it. The ultimate goal is to provide perfect value to the customer through a perfect value creation process that has zero waste.”
What is the difference between lean operations and traditional operations?
Traditional operations implement very few changes to improve efficiency. The whole concept of lean operations is devoted to continual improvement of workflows and processes, often through the increased use of technology, to reduce costs, eliminate waste, and increase revenue.
How can lean operations benefit an organization?
There are many ways lean operations can benefit a company including, but definitely not limited to:
The mission of continuous improvement delivers neverending ROIs and cost reductions
Lower costs across the supply chain
Lean operations take a just-in-time approach to inventory management and production output, saving energy, space, and time
More environmentally sustainable company with lower carbon emissions
More automation so employees can devote time to innovation
Faster output with higher quality
Better internal communications for a more engaged workforce
Lean embraces predictive maintenance and zero unplanned downtime
Stable workflows and business resilience
Greater agility and faster response to demand
What are the key steps to implementing lean operations?
There are several paths a company can take when adopting lean operations strategies. But here are a few general rules to becoming a lean organization:
Implement a mobile-first communication tool throughout your company for real-time, enterprise-wide connection. Effective communication is a critical part of lean operations. Poor communication is inefficient and expensive. Companies lose $37 billion every year from poor and miscommunication.
Begin to implement technology that will automate workflows. Use chatbots for employee-HR communication. Use AI to manage onboarding. Adopt IoT systems to connect equipment and enable predictive maintenance.
Train your staff on new processes and procedures and explain the purpose of lean management and its benefits. When they understand the why behind the changes and the benefits, they’ll have a greater stake in improving operations.
How long does it take to see results from lean operations implementation?
The timeframe to see the positive impacts of lean operations often depends on how far and fast a company goes on the lean journey. Investing in new technology and tools and change management procedures might not happen all at once. Some companies with limited budgets might take longer to get their whole operations on a lean track. Changes are not overnight, but once things are in a flow and everyone is on board and training for the new systems, companies can see results quickly by tracking predetermined KPIs (i.e. energy bills, production output.)
It’s important to include communication technology in the lean operations plan. If everything is moving at warp speed but manufacturing workers are still looking for their messages on a bulletin board, it defeats the whole purpose and slows everything down, and limits the benefits of a lean system.
What role does employee involvement play in lean operations success?
Lean management is much bigger than efficient workflows. It is a core part of company culture and it requires everyone to get on board and think with the same mindset. There needs to be a symbiotic relationship, where everyone is equally invested in achieving goals and willing to always think of how to do things better. The production worker has first-hand knowledge of the machinery and can give valuable feedback on what’s working and what’s not.
This is another reason why companies need a mobile-first communication strategy, something we also call a frontline success system. It enables two-way communication for a bottom-up approach that is inclusive of everyone. Lean operations are a group effort and require everyone to be involved.
Interested in learning more?
Join 1200+ companies transforming frontline work with Beekeeper. Start your journey today to make every task easier, every team stronger, and every shift smoother.