How to Boost Employee Productivity in the Age of Automation
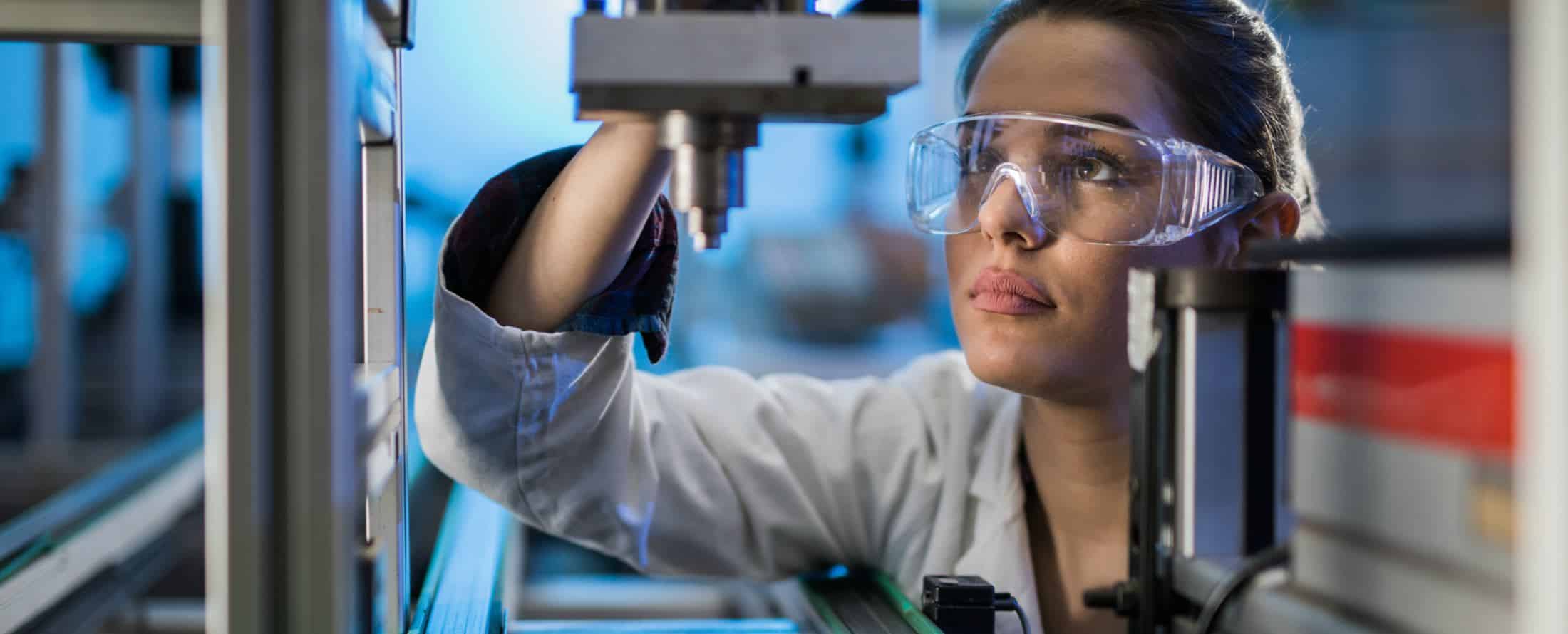
1830. Tailors are rioting in the streets of France, setting factories on fire to destroy the enemy—the sewing machine. They believed this advancement in clothing manufacturing threatened their livelihood. When the hysteria died down, the sewing machine actually increased employee productivity in the garment industry by 500%.
Learn how automation can support frontline workers in your manufacturing company.
Throughout history, new technologies have emerged that have disrupted manufacturing only to result in greater efficiency and higher output. Today, it’s automation. Robots, AI, 3D printing, augmented reality, and smart machines are running production lines. According to the World Economic Forum, by 2025, machines will be doing more than half of the tasks in global industries. But this automation will lead to a net gain of 58 million jobs across industries.
With predictions like that, it’s easy to understand why experts once predicted automation would be devastating for the manufacturing workforce. But in fact, just like previous advances in the industry, this evolution is creating an opportunity to boost employee productivity to new levels.
Embrace Automation and Watch Employee Productivity Soar
Automation has been a hot topic in the manufacturing world for the past decade. But even as more companies introduce robots and smart machines into their organizations, it’s still a big transition for employees, and it can lead to fear of job displacement.
Those fears and uncertainties can create fractured workflows. To create a smooth, seamless transition, explain to your employees why you’re automating systems, how technology will actually support their work, and the opportunity for professional growth as they move from the factory floor to other positions within the organization.
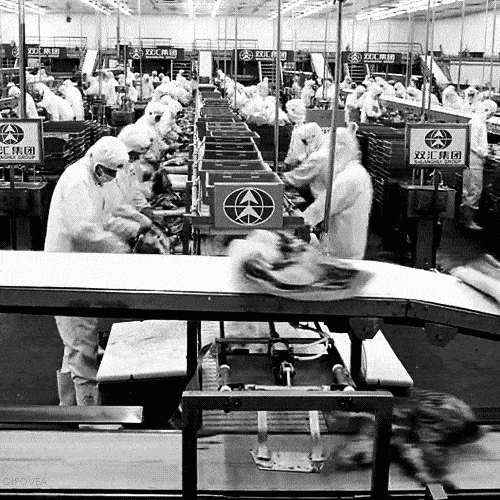
Automation is exciting. It’s an opportunity to restructure your operation, grow your business, and be more productive. Get employees on board from the start and they’ll work hard knowing they’re part of the team.
Provide Digital Tools for Maximum Productivity
Your employees need their own digital strategy to ramp up their productivity to match the momentum automation will bring to your operation. As you automate your production, give employees real-time digital tools that streamline communication and workflows to allow employees to work just as fast and efficiently as their digital counterparts.
While production line work was often a solitary, siloed profession, the next generation of manufacturing jobs requires an operational communication system that enables connectivity and alignment to do their jobs.
For example, digital managers need to send and receive communication to smart machines. Designers and engineers will need to collaborate to expand and diversify product lines. Equip them with the tools to perform their jobs that enable them to be as productive as possible.
Pro tip: As you automate production, upgrade your workforce tech, too. Give frontline workers their own cloud-based mobile communication tool.
Mobile workforce management software establishes a deep connectivity between an entire enterprise for a 360-degree view of manufacturing operations. It creates a channel for peer-to-peer communication and collaboration for a more innovative workplace. It enables bottom-up and top-down communication. Digital tools also allow leaders to track and analyze workforce metrics, like engagement and productivity.
Invest in Your Employees with Growth Opportunities
There is a preconceived notion that automation will force people out of jobs. There’s no question that machines can work faster and more efficiently than humans when it comes to rapid, repetitive production work. But there are things computers can’t do that manufacturing organizations need to survive, thrive, and grow. Automation isn’t pushing people out but it is changing the nature of manufacturing jobs.
With machines on cruise control, your human workforce needs a new purpose. In fact, according to McKinsey Global Institute estimates that by 2030, 375 million people in the world’s workforce will need to shift career gears and enhance their skills due to automation.
Pro tip: Find the skills gap in your operation and train your employees for new positions.
Train your employees for jobs computers can’t do but that your organization needs to be competitive. Humans are capable of critical thinking, negotiating, strategizing, collaborating, creating, designing, and problem solving. Reorganize your business structure to create jobs that will reinvigorate your workforce and create opportunities for team efficiency, collaboration, and innovation to promote business expansion.
Those include:
- Software engineers and Programmers
- Customer service
- R&D, product development
- Data analysts
- Sales and marketing
- Customer service
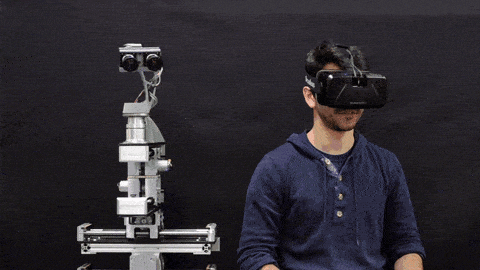
Not only will your workforce have skills that can support productivity and growth, simply investing in your employees with educational opportunities will let them know they are a valued part of your organization which will result in a hard-working team.
To reskill employees, business leaders can utilize a mobile workforce management platform to support in-house training programs. Using a digital solution allows employees to manage when and where they conduct their online training so it fits within their lives. Autonomy is a big-ticket item when it comes to building an engaged, productive workforce.
Employees can better serve your company in jobs that aren’t as tedious. When you transition employees from lower-skilled work to high-impact careers with cerebral tasks—imagining, innovating, creating, coding—they’ll have a new sense of purpose in their work that they find more exciting and engaging. They’ll recognize opportunities for growth in their personal lives and within your organization and will work hard to achieve personal goals.
Another factor to consider as you retrain your workforce in the face of automation is workplace safety. In positions that are less physically-demanding, employees have a reduced risk of on-the-job injuries. This lowers workforce stress levels, improves mental well-being, and increases employee life cycles.
Automate Administrative Functions
As your production line hums along to the rhythm of robots and machines and your workforce is busy in their new roles, it’s essential to automate the rest of your organization to keep every element of the operation running smoothly.
In other words, if you automate your production while your admin teams still use overstuffed filing cabinets, you’ll hinder the progress of your organization. A mobile-first digital workplace creates an employee portal to streamline all communication within a company to maximize employee productivity and team efficiency.
- Automate HR functions, like payroll.
- Choose a platform that enables shift scheduling so every worker has access to their own hours and the ability to swap shifts and connect with peers directly for work coverage.
- Have all safety manuals and documents accessible online so workers can access them immediately in case of an emergency.
- Bring your onboarding online so new employees work straight from the platform.
The age of automation is an exciting time for manufacturing. Once you embrace this new way of operating, leverage technology to maximize workforce productivity. You’ll see greater output and a better employee experience.
Learn how automating your manufacturing operations can lead to a boost in employee productivity. Download our Manufacturing Industry Trends for 2020 white paper.
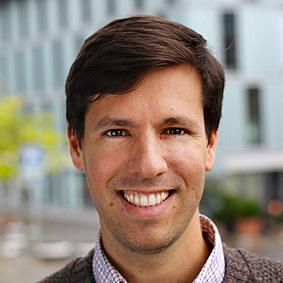
About the author
Daniel Sztutwojner
Chief Customer officer
Daniel Sztutwojner, Chief Customer Officer at Beekeeper, focuses on the acquisition of new business and the customer-centric approach of the company. Prior to Beekeeper, Daniel worked on several projects in Innovation and Technology and co-founded a web startup that took him around the world, mainly to Israel and the U.S. Daniel holds a BSc and MSc in Applied Mathematics from ETH Zurich.
Interested in learning more?
Join 1200+ companies transforming frontline work with Beekeeper. Start your journey today to make every task easier, every team stronger, and every shift smoother.