If your employees are doing this, it’s safe to say they may have too much downtime on their hands.
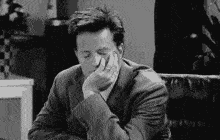
Many industries have experienced a rise in downtime because of COVID-19. Learn how to adapt to the next normal with our recovery roadmap.
But what can you do about it?
Let’s dig into what downtime means, why it matters, and how it could be hurting your business.
What Is Downtime At Work?
To better understand what is downtime at work and how to best manage it to make your team more productive, let’s start from the beginning.
Downtime Definition and Downtime Meaning
The Business Dictionary describes the downtime definition as:
Period during which an equipment or machine is not functional or cannot work. It may be due to technical failure, machine adjustment, maintenance, or non-availability of inputs such as materials, labor, power.”
This definition infers downtime is specific to more labor-intensive industries, such as manufacturing and construction.
Yet, companies across many verticals are challenged with maximizing employee value during downtime.
We define downtime as a time when employees are involuntarily idle in their work tasks, due to equipment or technological malfunction, project bottlenecks, or a lower volume of in-person customer interaction.
Why Downtime Is a Big Deal
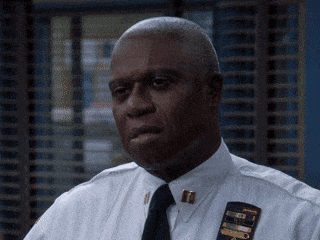
Downtime costs U.S. companies a staggering $100 billion each year.
That’s a large chunk of change that, in today’s post-COVID environment, many companies cannot afford.
Companies that better manage downtime:
- Are more flexible to changing situations
- Have a more informed and productive workforce
- Are more operationally efficient
- Reduce associated costs with downtime, whether planned or unplanned
How to Manage Downtime
From asset-heavy businesses to professional services – everyone struggles with downtime.
There are two main culprits that cause downtime for employees..
Planned Downtime
Every business has a busy and a slow period. Knowing when these demand cycles occur is critical to effectively managing downtime.
Is your business seasonal? Are there times your store is busier than others?
Companies that have a firm grasp on their demand cycles are often able to find new ways for employees to remain productive even when times are slow.
Unplanned Downtime
The Achilles heel of downtime is when it happens spur of the moment, when companies are less prepared to address quickly.
Unplanned downtime can include:
- Machinery malfunction. Machines break down all the time. When they do, companies that don’t have the capacity to shift their employees to a different production line or task will accumulate downtime costs.
- Network crash. In today’s tech-heavy world, it’s incredibly frustrating when everything grinds to a halt because the internet goes down. Depending on how long the outage lasts, employees can wind up with a lot of free time on their hands.
- Workload bottlenecks. Occasionally work gets stuck in someone else’s inbox. Downtime occurs when an employee has completed their work, but they don’t know what to do next.
- Disaster or crisis situations. No one knows when disaster will strike. Just take a look at 2020. Yet, having a solid business continuity and disaster recovery plan in place can help ensure there is as little downtime as possible.
Ways To Reduce Downtime
When it comes to reducing employee downtime, companies need a toolbox of tips for minimizing slow periods and the financial impact they can have on your business.
Here are some of our favorites.
Prepare!
Whether you know downtime is coming or not, having a risk mitigation plan in place is a must.
In industries like manufacturing, it’s essential to understand your annual production cycle so you can plan for the necessary downtime.
For example, if your business peaks in the summer, you’ll want to have necessary maintenance done in the winter. During that maintenance time, have a plan in place to re-allocate labor and avoid downtime in your facility.
Whereas for unplanned downtime, make sure you have the tools and processes in place to address likely situations.
Establish a Mobile-First Communication Method
In times of crisis, you need to be able to reach employees fast. Not only for the benefit of their health and safety, but to give them instructions when needed.
A mobile-friendly employee communication platform, like Beekeeper, gives every employee instant access to important company information, 1:1 and group messaging, and real-time push notifications from any location.
Adopt New Technology and Tools
Reduce downtime by utilizing new tools that keep you one step ahead.
For example: In manufacturing, machines now have internal sensors that notify workers when maintenance is needed. With a real-time alert and response system, the technology of predictive maintenance can catch mechanical failures before they happen and reduce overall downtime.
Embrace a Flexible IT Infrastructure
The SaaS vs. on-premise debate is nothing new.
With on-premise software, the user is responsible for ensuring that timely software updates and data backups are done to prevent downtime, service interruptions, and other operational issues.
However, companies can reduce downtime by moving their systems to the cloud. They can then fix problems as they arise from any location.
Industries That Can Benefit From Reducing Downtime
Many different industries are financially, socially, and operationally impacted by downtime.
Industries that could benefit from better managing and reducing employee downtime are:
Manufacturing
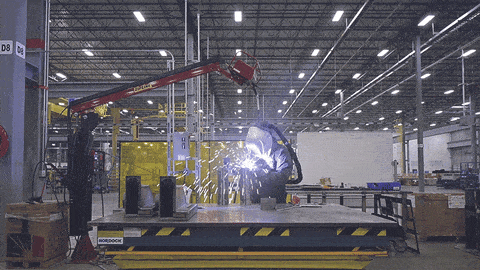
Manufacturing is heavily impacted by machinery and employee downtime. Yet, it’s also an industry best equipped to create a comprehensive planned downtime schedule given the rise in smart machines and regular production cycles.
According to a recent study,
- 82% of companies have experienced downtime over the past three years
- Unplanned downtime costs companies $250,00 per hour
- Zero unplanned downtime is now the top priority or a high priority for 72% of organizations
Retail
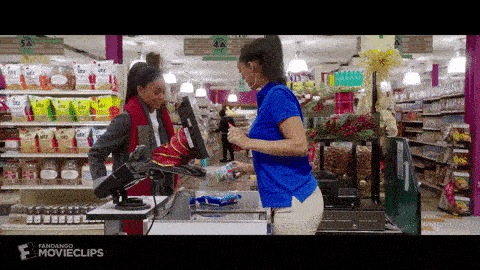
The retail industry has been hit hard by COVID-19, which means every productive minute counts now more than ever. Retailers typically experience downtime because of:
- Network disruptions
- Slow customer foot traffic
- Overstaffing
To reduce downtime and the subsequent escalating labor costs, retailers need to be able to pivot quickly, no matter the reason.
Hospitality
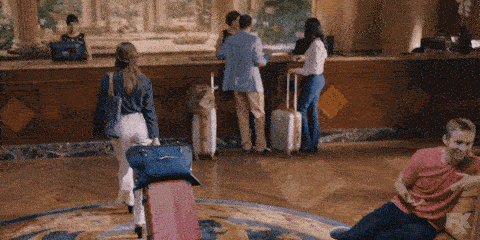
The hospitality industry, like many others, is a well-oiled machine. Yet, downtime does happen and is typically caused by unplanned events, such as network disruptions or in 2020’s case, a global pandemic.
During COVID-19, the Mandarin Oriental Hotel Group used its Beekeeper mobile communication app to stay in touch with employees. While furloughed employees were on leave, the hotelier was still able to share information and employee development opportunities for those workers to take advantage of during their downtime.
Best Practices and Strategies for Managing Downtime
Downtime can be frustrating, but it’s an excellent opportunity to make your business more productive during uncertain times.
Here are five best practices and strategies to help tackle employee downtime within your organization.
1. Offer Appointment Scheduling
A highly effective way to reduce downtime, particularly for foot traffic-heavy industries like retail and banking, is by offering appointments that are scheduled well in advance.
By allowing customers to request dedicated time to spend in your business location, companies can:
- Smooth out the flow between busy and not busy periods
- Counterbalance the slow times by making pre-appointed meetings when your business is less likely to be busy
2. Give Access To On-Demand Training Programs
When the unexpected happens – a machine goes down, or the internet is acting up again – have a platform in place that allows employees to pick up training programs on the fly.
Sometimes you can’t stop unplanned downtime, but you can make it an opportunity for employees to better contribute by developing new skills.
3. Optimize Processes With New Technology
Take advantage of new technology that can streamline processes and redirect your workforce where they can make the most impact.
For example, digital tools are maximizing employee productivity in manufacturing, while retail analytics are helping stores better understand their busy and slow times.
4. Elevate Internal Communication Platforms
Frontline employees who are most impacted by downtime need more dynamic communication channels to stay connected with their organization. Particularly if downtime is the result of network issues, employees need to know how to continue to serve customers best.
Mobile-first employee communication methods, like Beekeeper, give employees access to information they need on the devices they use every day.
5. Keep An Agile Frame(work) of Mind
At the end of the day, unplanned downtime happens in any industry. That’s why companies need to remain flexible and always have a business continuity plan in place in case it happens at the most inopportune times.
Most Frequently Asked Questions
Is downtime at work common?
Yes, downtime costs U.S. companies a staggering $100 billion each year. That’s a large chunk of change that, in today’s post-COVID environment, many companies cannot afford.
What is downtime at work?
It is a period during which an equipment or machine is not functional or cannot work. It may be due to technical failure, machine adjustment, maintenance, or non-availability of inputs such as materials, labor, power.