4 Novel Ways to Transform Your Factory into a Green Manufacturing Plant
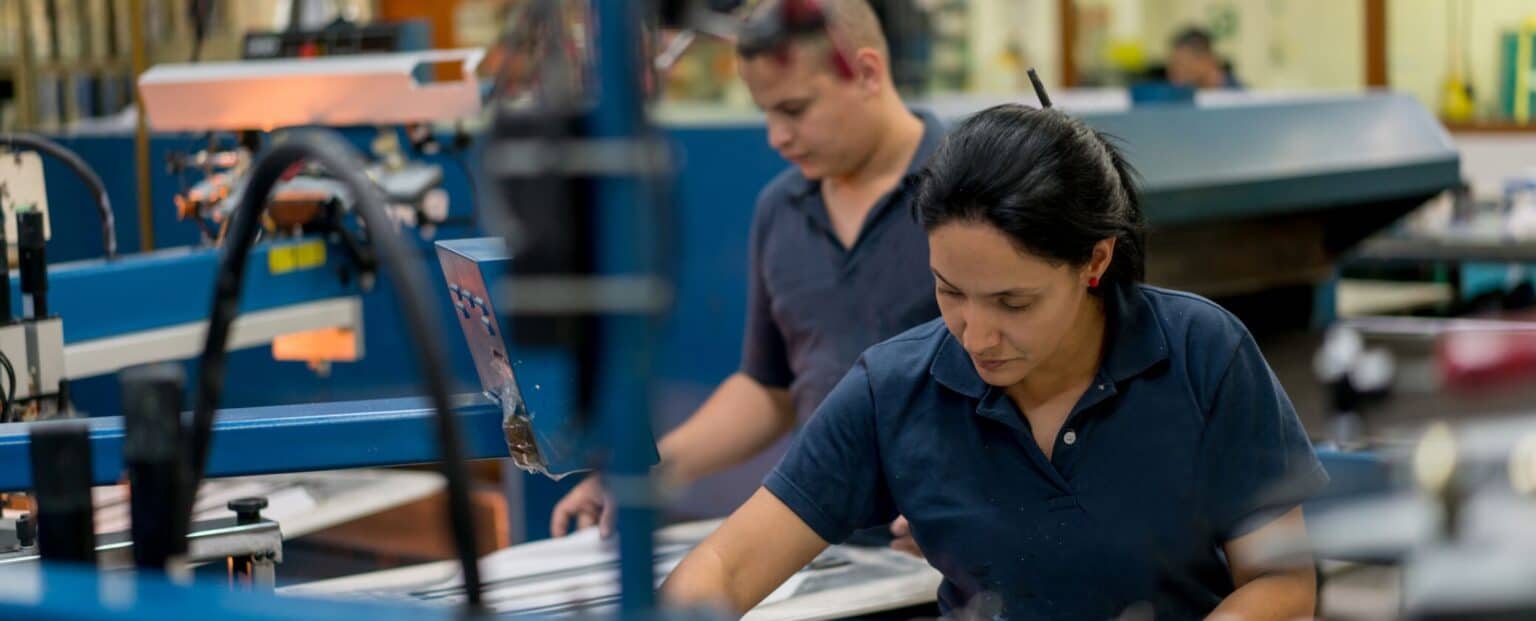
Everyone is “going green” nowadays, from solar-powered USB bikinis to repurposing children’s artwork.
And manufacturing companies are leading the way.
With around 315 million manufacturing workers worldwide, companies are figuring out new ways to create green manufacturing plants to retain employees and keep job satisfaction high.
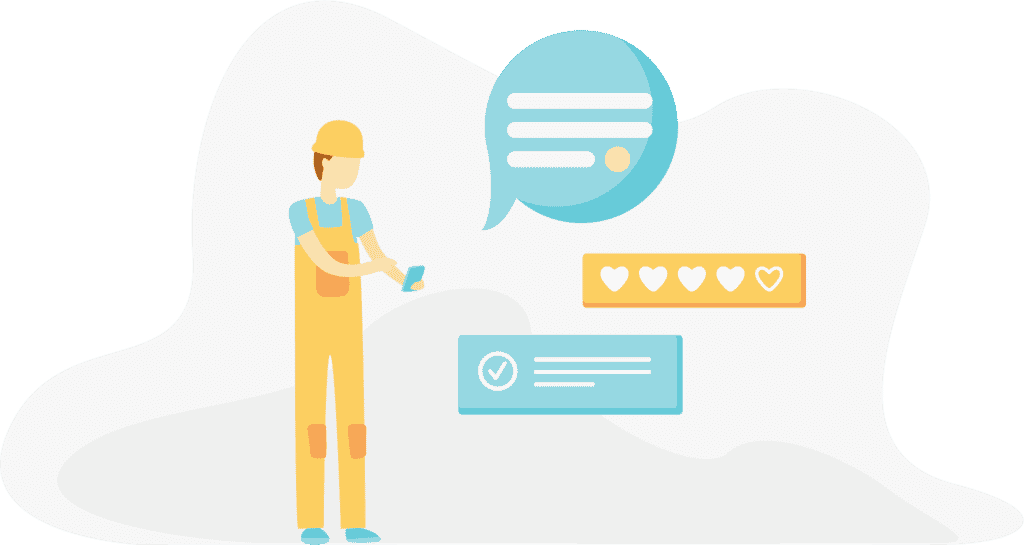
Legal needs, rules, and regulations, and reducing the carbon footprint aren’t the only ways to encourage going green. There are several monetary incentives to create green manufacturing plants as well, such as tax savings, reduced costs, and increased productivity.
According to McKinsey & Company, using the right technology in manufacturing will lower costs in the range of $200 to $600 billion across the industry. It really pays to go green.
With that in mind, let’s take a look at how manufacturing companies can go green and save money at the same time.
1. Use Circular Manufacturing to Save Energy and Reduce Waste
Manufacturing equipment and companies are becoming more sustainable by creating a regenerative model that fuels their facilities. Circular manufacturing is also called lean manufacturing and it includes:
- Recovering resources and repurposing the materials
- Lending equipment as a part of the sharing economy
- Using predictive maintenance to increase the lifetime value and durability of machines and equipment
- Switching to a renewable power source that provides energy to the factories
Circular manufacturing is a green solution with a three-fold win.
- It follows “green” rules and regulations.
- It’s good for the planet
- It’s what the end customers want
Instead of purchasing raw materials for themselves, green plants simply use the waste produced by another plant (water, energy, and other resources) to meet their needs.
A great example of this is Kalundborg Symbiosis — a group of nine manufacturing companies from Denmark who have been trading waste since 1961. Annually, they save 24 million EUR and reduce carbon emission by 635,000 tons.
2. Implement Safety Measures by Utilizing Automation Tools, AI, IoT, and Cobots
The cloud-based technology, alongside the Internet of Things (IoT) will provide the ability for humans to work alongside automation tools, AI, and cobots, and is one of the ways for companies to go green.
Cobots, or collaborative robots, are intended to work alongside humans in a shared space to complete tasks. IoT will help us navigate the entire manufacturing process, enabling humans to coordinate dangerous jobs with robots. And this is where cobots come into play.
The manufacturing industry has some of the highest rates of on-the-job safety incidents, with an estimated average of 400,000 non-fatal injuries per year. To avoid these injuries and prevent further harm, AI and cobots will perform dangerous tasks and that will decrease the number of injuries per year.
That will turn factories into safer work environments.
But that’s not the only benefit. The increased safety measures will result in less downtime for employees and it will reduce the machine reparation downtime since they will go through predictive maintenance. Productivity will rise (40% by 2035) and there won’t be the (energy) costs of restarting the machines, all the while creating a safer work environment for humans.
But that can only be fully implemented with digitized, internal communication.
3. Digitize Internal Communication
By making all internal communication 100% digital, you’re not only saving tons of paper each year, but you’re also making your overall operations more efficient.
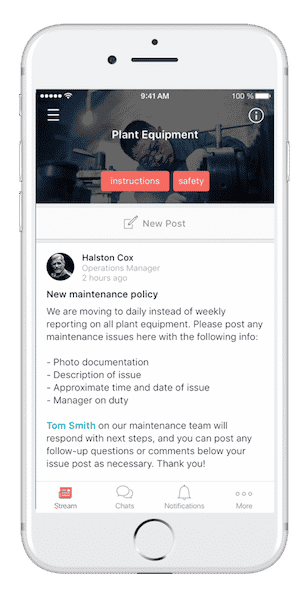
Better communication improves operations. And real-time, mobile communication is becoming an increasingly popular way to enable frontline manufacturing workers.
Communicating in real-time has multiple benefits:
- Alerting other workers of any hazards and equipment failures which is critical for safety
- You can keep the manufacturing pace high by communicating important messages (like shift-changes) fast
- It saves time and money by being able to send (and receive) messages instantly (no bulletin boards)
- Improves coordination between employees
- Improves coordination between employees and managers
- Enables employees to manage AI, robots, and cobots using mobile tech tools
According to Deloitte, 77% of manufacturing companies see “online collaboration platforms” as tools that will significantly impact their workforce in the next five years.
A digitally connected workforce is faster, safer, more productive, and greener.
And the mobile-first communication tools allow employees to become partners with their peers, managers, and even machines.
This also rebrands the manufacturing plants into green, tech-advanced plants that attract the attention of the new people inside the workforce— millennials.
4. Implement Eco-friendly Products
According to the U.S. Bureau of Labor Statistics, millennials will make up around 75% of the entire workforce by 2030.
So in a matter of 10 years, you will have a workforce that deeply cares about sustainability in the workplace, and companies will have to adjust how they operate to attract the next generation of manufacturing workers.
One of the best ways to encourage going green in a manufacturing plant is to implement eco-friendly products. Not only are these products more sustainable, but they also cut costs for the company at the same time.
Lighting systems are a great example of this.
Being mindful of lighting systems can really affect your monthly electricity bill and even save up on energy. One way to do this is to change incandescent lights into LED lights. Not only are they more effective (last 25 times longer than incandescent), but they are a green solution since they use 75% less energy than regular lights. That makes a massive difference on the scale of manufacturing plants, especially in the long run.
Taking small steps towards creating a more sustainably run manufacturing plant can have a big impact in the long run and get your company that much closer to being completely green.
Most Frequently Asked Questions
What is a green factory?
A Green Factory is equipped with eco-friendly machines, has a low gas emission, and a low energy consumption.
How can factories go green?
- Implement Eco-friendly Products
- Use Circular Manufacturing to Save Energy and Reduce Waste
- Implement Safety Measures by Utilizing Automation Tools, AI, IoT, and Cobots
- Digitize Internal Communication

About the author
Andreas Slotosch
Chief Growth Officer
Andreas is one of the Co-Founders and VP of Growth at Beekeeper. Prior to Beekeeper, he was involved in various web start-ups and worked for several international companies in the area of business development and marketing. Andreas is a graduate of the University of St. Gallen and author of numerous blogs and book contributions on the topic of mobile internal communication and employee engagement.