What Are Manufacturing Goals and Objectives? 5 Tips for Setting and Achieving Them
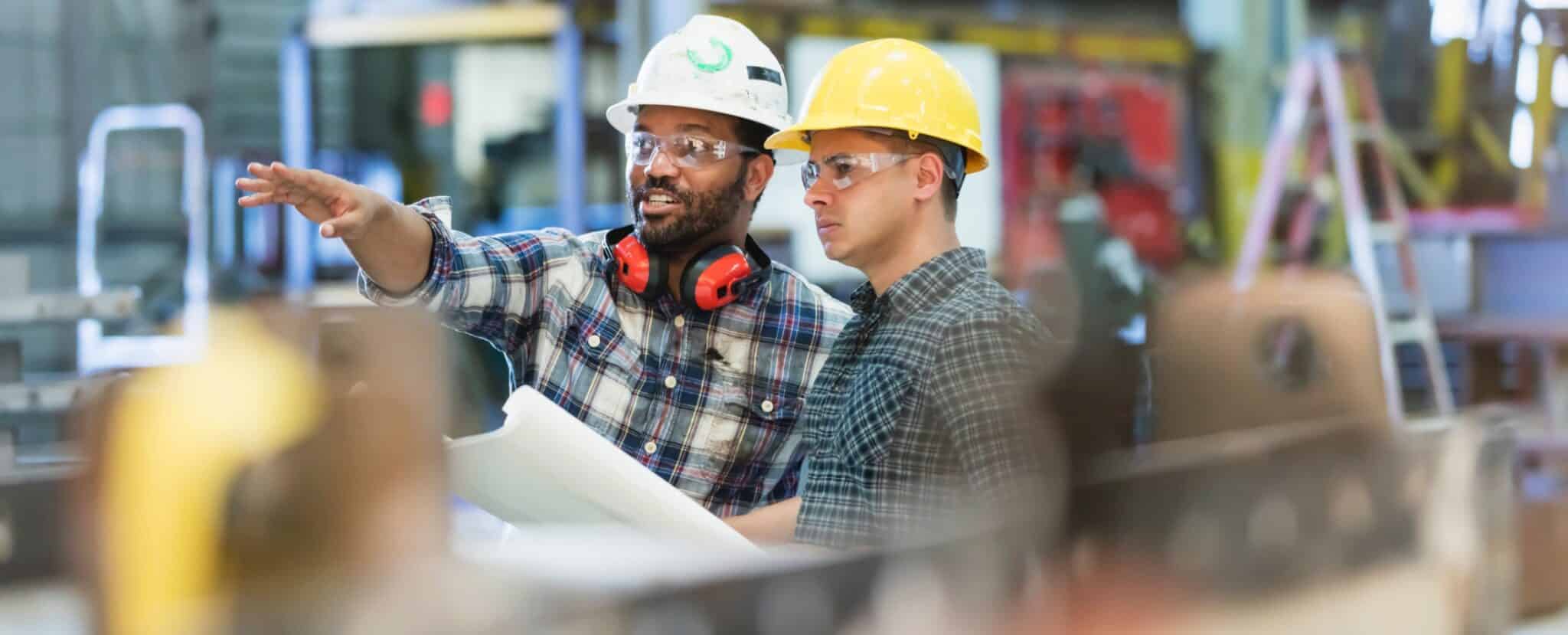
From day-to-day tasks to long-range planning, setting manufacturing goals and objectives can help a company refine its operation, improve efficiency, and reach the pinnacle of business success—long-term, sustainable growth.
Maximize uptime. Minimize downtime. Boost productivity by optimizing maintenance management.
Having a clear direction of where you want to take your company is the foundation of any business plan. But what goals and objectives should you set for your own manufacturing company?
Let’s start with the basics.
What Are Manufacturing Goals and Objectives?
Manufacturing goals and objectives are the accomplishments a company would like to achieve and the steps they plan to take to get there. Goals and objectives each play a big part in aligning employees to the company’s overall mission and create a road map to follow on a day to day basis.
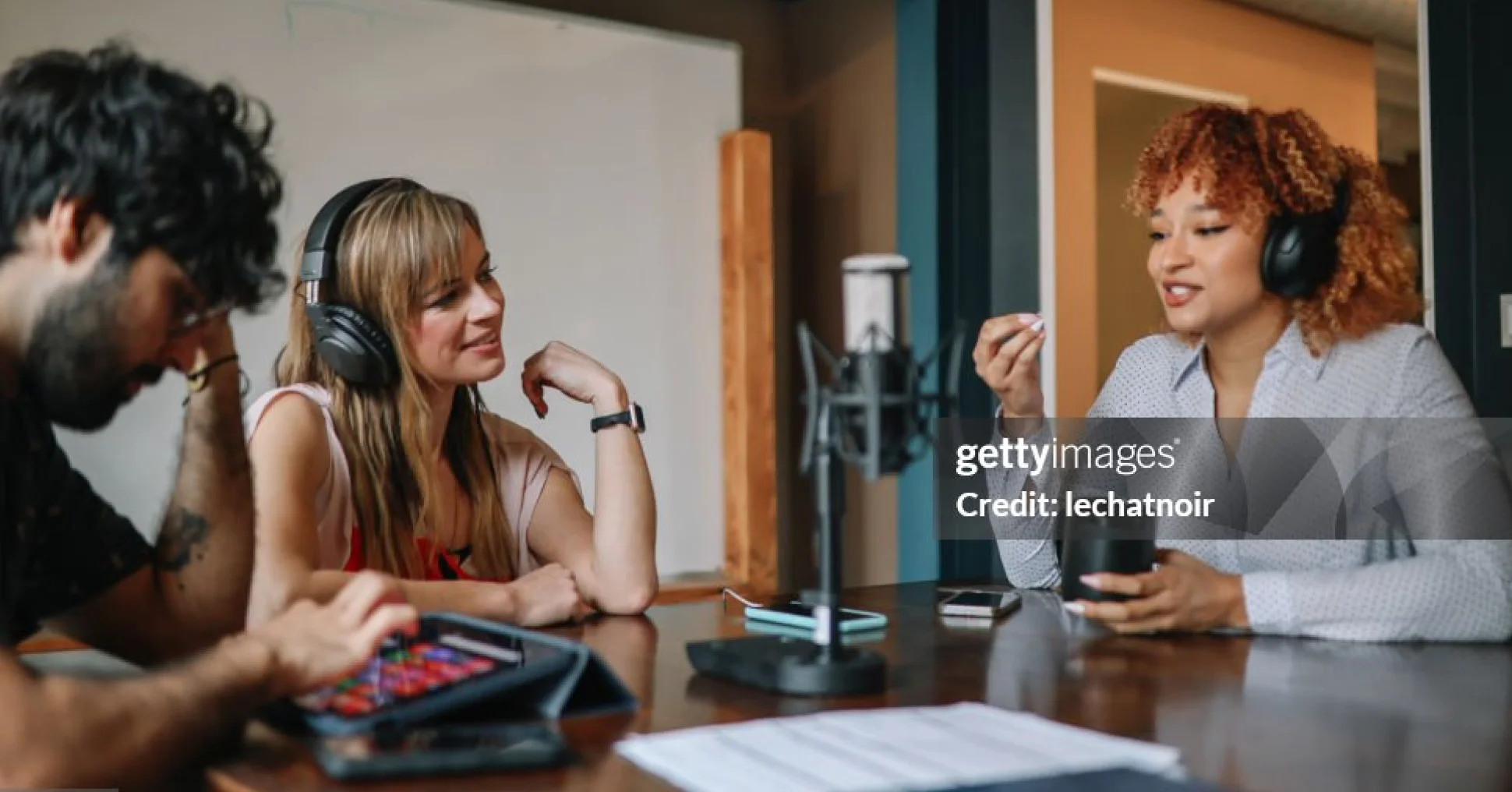
2. Simplify onboarding for you and your employees
Every day, we talk to HR leaders who are drowning in paperwork and endless requests. Automation can be your lifeline. Take Resorts World Las Vegas as an example. They had the challenge of onboarding 5,000 new employees within just a few weeks. So they brought all SOPs and policies into a mobile document library, then created a system for assigning training and monitoring completions. Workers suddenly had everything they needed to do their jobs at the tip of their fingertips.
This doesn’t have to be rocket science. You can start by:
- Sending automatic onboarding messages to incoming new hires
- Emailing HR with submitted paperwork on a weekly schedule
- Creating a simple approval process for PTO requests
None of it has to be built from scratch. Our product team leveraged best practices from our customers and turned them into onboarding templates you can quickly customize to your needs.
Goals are the big picture outcomes you want to achieve with your company.
Objectives are the measurable steps and actions you take to reach those goals.
Think of goals as your destination and objectives as your mile markers. Despite their different purposes, both are instrumental in creating more efficient workflows and increasing quality, safety, and productivity, and ultimately boosting the bottom line.
For example, a steel manufacturer might have a goal of having a 15% market share of the U.S. steel exports. In order to achieve that, they may set objectives that help them get there, like increasing productivity by connecting the workforce through a digital collaboration tool.
Manufacturing Goals and Objectives Examples Companies Should Follow
Manufacturing objectives and goals should represent a cross-section of your organization. From HR to marketing, sales to production, every department in your manufacturing company should have targets they need to hit. Together, this broad set of goals and objectives will help your company realize greater success and help you reach your desired revenue.
Here are some examples of manufacturing goals and objectives to include in your company’s long term planning:
- Workforce wellbeing: It’s no secret that the happiness and wellbeing of your workforce is directly linked to company growth and success. Whether it’s through flexible schedules, advancement opportunities, or free lunches, there are many different ways companies can create objectives that result in happier workers. Organizations that take care of their employees are rewarded with lower turnover and higher engagement.
- Consistent, manageable growth: While growth can happen organically, companies should create strategies to deliberately set new targets. But leaders should set realistic expectations. Setting growth goals that are too ambitious could result in delayed production schedules and delivery that negatively impacts the customer experience.
- Greater business agility: Manufacturing operations are rooted in longstanding traditions, which means they can be resistant to change and slow to adopt new processes. But high-performing companies can easily adapt to change, so your objectives and goals should contribute to greater business agility.
- Digital transformation: Manufacturing led the charge during the Industrial Revolution. Now, the industry lags behind in digital maturity, especially when it comes to enterprise-wide tools. Companies should set goals to increase their digital communication capabilities that can create opportunities for collaboration, productivity and growth.
- Manufacturing maintenance objectives and goals: A large part of manufacturing inefficiency and wasteful spending occurs due to equipment failure or malfunction.
This unplanned downtime can cost companies up to $250,000 every hour.
Companies should implement steps towards becoming smart factories, automating processes through smart machines that can self-regulate and keep workflows running seamlessly.
Challenges When Setting Manufacturing Goals and Objectives
When doing your long-range planning, you may encounter some hiccups and discover operational inefficiencies. But navigating these challenges will ultimately make your company more resilient.
Goal-setting is more important than ever for manufacturers. There’s already significant strain on existing production systems from surging demand as the economy begins its recovery, leading to pressure on manufacturers to add automation and other advanced technologies to remain competitive. But guess what? Those newer technologies require advanced skills for both operators and maintenance personnel.
Having the right goals in place for desired business growth and capital investment will drive equally vital staffing and training goals to support that growth. Right now the training of skilled workers isn’t keeping pace with demand, so knowing your personnel needs well in advance will make your recruitment efforts far more likely to succeed. And it will drive the right internal training efforts to keep your current workforce up to speed as well.
– Jim Vinoski Forbes writer and manufacturing expert
Here are a few challenges you might experience when determining the goals and objectives for your manufacturing company:
Making Safety a Top Priority
It’s easy to get tunnel vision when goal setting. But in manufacturing, which has a higher incident rate than other industries, it’s important to look at how every decision will impact safety. For instance, when a company is looking to reduce operating expenses, make sure budget restructuring does not sacrifice safety for cost. Spending more upfront can save you money in the long run.
One example—investing in mobile communication for your employees to give them equal access to information can reduce safety costs by more than $40,000.
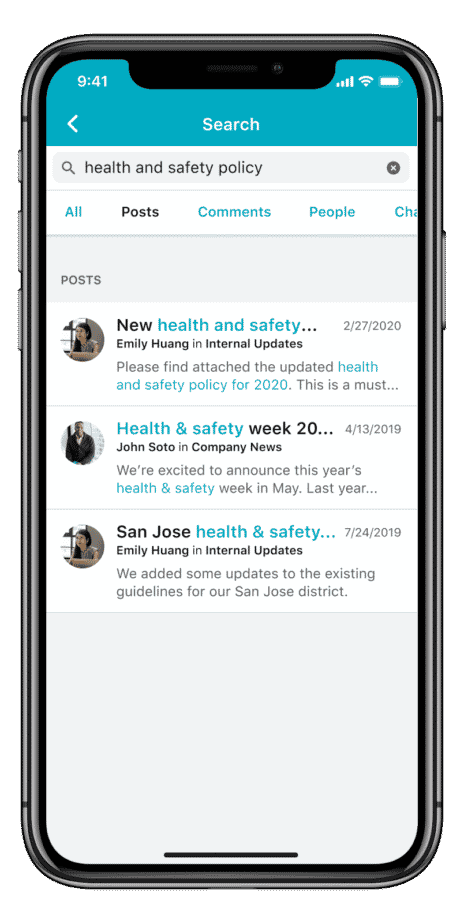
Lack of Accurate Data
Your goals and objectives should be as specific as possible. This means setting defined target numbers. But in order to really know what your company is capable of achieving, you need to understand where you’re at now. Make sure you have a productivity and collaboration platform that collects data in one place and delivers metrics in real-time.
Supply Chain Management
You can do your best to set goals and deadlines, but some issues will be out of your control and can throw you off schedule. Streamline your supply chain so there are fewer moving parts that can disrupt your operation and stop your progress toward achieving goals.
Labor Shortage and Skills Gap
Manufacturers have been facing a labor crisis. There is both a shortage of skilled workers in today’s Industry 4.0 factories and an overall shortage of people entering the manufacturing field. Reaching goals and objectives will take longer without the internal support needed to achieve them. Companies should focus on recruiting the next generation of workers who are looking for digitally progressive companies to build a robust, skilled team.
Ability to Communicate Goals
Reaching goals is a company-wide effort, and leaders should align their entire workforce to the mission. In manufacturing, most workers are on the frontlines without access to work email. A mobile communication tool enables leaders to include everyone on the shared objectives and assign, and track, individual tasks to workers directly. It creates two-way communication so workers can provide updates on their progress.
10 Reasons You Should Set Manufacturing Goals and Objectives
Manufacturing is an industry with many moving parts which must be in sync to perform complex functions. A company should focus on improving the performance of each individual part by setting specific targets they want to reach.
Having set goals and objectives can help a manufacturing company:
- Easily navigate challenges
- Align an organization on a clearly defined path
- Meet customer expectations and delivery targets
- Create a streamlined supply chain
- Reduce waste
- Boost innovation
- Increase productivity
- Bring the purpose of the business into focus
- Create a common mission and increase collaboration
- Track your progress on your business journey
5 Tips for Setting Manufacturing Goals and Objectives
While every company will have a unique set of circumstances that will guide what goals and objectives they set, here are five general tips to take into consideration:
- Make the Goals Specific
Goals and objectives need to be specific. For example, instead of “increase revenue,” set an actual target like, “increase revenue by $150,000 next quarter.” Having a specific number helps align expectations and gets every department and employee working towards the same target. - Track and Measure Your Progress
On any given day you should know if your company is on track to reach its target. You should measure every objective so you can adjust strategies as needed to help reach your final goal. Using a communication platform creates one centralized location where workers can upload reports and spreadsheets to track progress. - Include Everyone
Manufacturing goals and objectives can only be achieved when every employee understands how their job plays a part in achieving them. Leaders need to be transparent and share goals and progress with their entire team. 69% of leaders believe that when business goals are communicated and understood across an entire company it helps increase employee engagement. Assign employees tasks that play to their strengths. Gallup suggests “Based on your employees’ roles and strengths, place them in positions that help the team achieve quality success in your goals.” - Set Deadlines (and stick to them)
Whenever possible, include a deadline for goals and objectives. This sets better parameters for your employees. It allows people to create schedules and use time management skills to accomplish their tasks related to company-wide goals. Avoid getting into the habit of extending deadlines unless absolutely necessary. - Create a Goal-Oriented Culture
When you accomplish objectives and reach goals, celebrate those major milestones. But remember that long-term, sustainable growth comes from setting goals, reaching them, and then setting new ones. Create that mindset in your employees, too. You’ll create a goal-oriented culture where everyone is driven by the same mission.
Want to streamline your maintenance and inspection process? Get access to our template library below!
Get the Checklist
Most Frequently Asked Questions
What are some examples of goals and objectives?
- Workforce wellbeing
- Consistent, manageable growth
- Greater business agility
- Digital transformation
- Manufacturing maintenance objectives and goals
How do you form goals for a manufacturing company?
To set goals, it is extremely important to make the goals specific and to track the progress. In addition, the goals should be shared with everyone so that every employee feels included. Finally, setting deadlines and creating a goal-oriented culture also help to form goals.
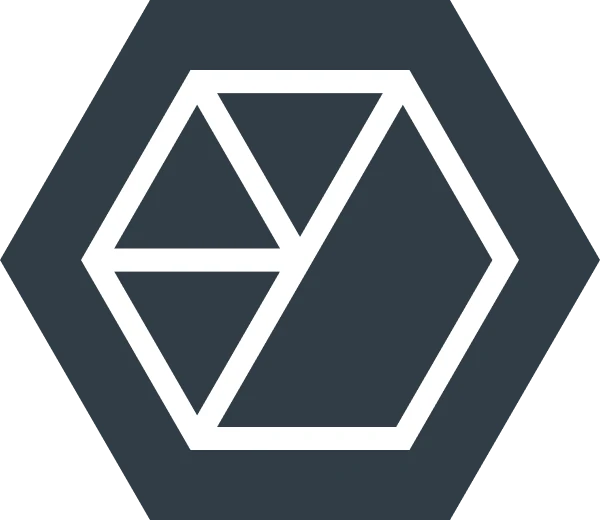
About the author
Beekeeper
We make frontline lives easier, work safer, and teams more connected so businesses can reach new heights. At Beekeeper, we’re dedicated to making frontline lives easier by connecting workers with the tools, support, and information they need to feel valued, do their best work, and drive the business forward.