Operational Excellence? Definitions, Tips, and Best Practices Revealed
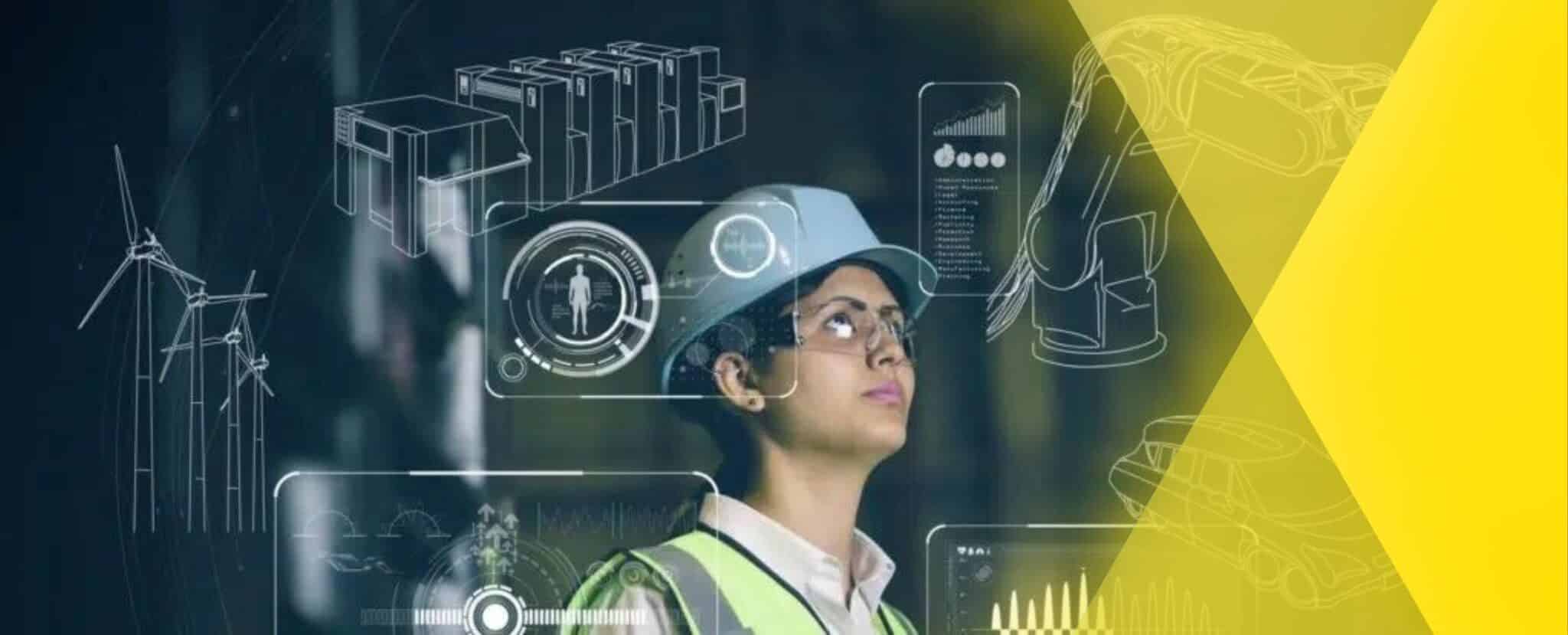
Table of contents
- What Is Operational Excellence?
- What Are the Operational Goals?
- Difference Between Operational Excellence
- Why Does Operational Excellence Matter?
- Why Does Operational Excellence Matter?
- Operational Excellence Examples
- Which Industries Can Benefit from Operational Excellence
- Operational Excellence Best Practices and Strategies
- Frequently Asked Questions About Operational Excellence
- Operational Excellence is Key to Improving Employee Engagement and Customer Satisfaction! Download our Maintenance & Inspections Checklists and Templates to Streamline Your Operations Today
Achieving operational excellence is an organizational journey, but sometimes it can feel like a never-ending quest for hidden treasures.
Maximize uptime. Minimize downtime with Beekeeper’s Maintenance Management Package.
Operational excellence is an essential strategy to sustain growth while staying ahead of the competition.
But in reality, it’s a vague concept that leaves many of us looking like this:
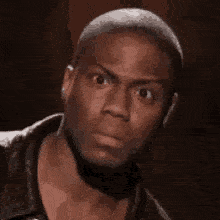
Let’s uncover the principles of operational excellence and why it’s important. Then we’ll look at a couple of operational excellence examples showing how companies address it on their own terms.
What Is Operational Excellence?
Operational excellence is a business philosophy that focuses on continuous improvement and the optimization of business processes and systems to achieve better results. It aims to increase efficiency, reduce waste and costs, and improve quality and customer satisfaction.
Overall excellence leads to next-level performance because your operational house is in order. In truth, your operational excellence meaning can be whatever your company decides it is.
Many believe the core principles of operational excellence mean performing better than your peers through growing revenue and lowering Operational Costs. It’s also a mentality deeply ingrained in your company culture that empowers your workforce for continuous improvement.
According to BTOES (Business Transformation & Operational Excellence):
Companies in pursuit of operational excellence do two things significantly differently than other companies: they manage their business and operational processes systematically and invest in developing the right culture.”
What Are the Operational Goals?
Operational excellence is based on methodologies such as Six Sigma, Lean Management, Kaizen, and the Shingo Model. Each method has its own set of core principles to help guide your decisions.
That said, it’s best practice to establish clear goals when implementing any new process or program in your business. Established goals make it easier to capture your ROI.
Let’s look at what are the operational goals types to consider when building your plan.
1. Operational-Oriented Goals
Operational goals focus on enhancing company productivity and improving product or service quality. Goal examples are increasing safety measures and enhancing product or service flexibility.
2. Financial-Oriented Goals
Finance goals aim to improve financial metrics visible through financial data analytics. These continuous improvements are the result of better operations, stronger customer relationships, and better value to the customer. They often come as a result of growing profits, cutting costs, and generating free cash flow.
3. People-Oriented Goals
Finally, people-oriented goals concentrate on workforce and cultural efforts that play a critical role in making an organization operationally excellent. Examples include growing employee engagement in operational excellence efforts, increasing skill training, and maximizing employee productivity.
Difference Between Operational Excellence
There are a few established operational excellence methodologies that are worth keeping in mind:
Shingo Model
The Shingo Model is an operational excellence methodology that was developed by an industrial engineer and Toyota production system expert Dr. Shigeo Shingo.
The Shingo Model is based on the principles of lean manufacturing and focuses on creating a culture of continuous improvement. It consists of ten core principles that are essential to improve operational excellence. These principles are divided into four categories: Cultural Enablers, Continuous Improvement, Enterprise Alignment, and Results.
- Cultural Enablers include principles like Respect for Every Individual, Continuous Improvement, and Empowering People. These are focused on creating a culture of respect, trust, and collaboration within the organization. They encourage employees to take ownership of their work and to continuously look for ways to improve their processes.
- Continuous Improvement includes principles such as Flow and Pull, Seek Perfection, and Create Constancy of Purpose. These are focused on improving the flow of materials and information through the organization, reducing waste, and continuously seeking ways to improve processes. They encourage organizations to focus on long-term goals and to strive to perfect their processes.
- Enterprise Alignment includes principles such as Focus on Process, Think Systematically, and Create Value for the Customer. These are focused on aligning the organization’s goals and processes with the needs of its customers. They encourage organizations to think systematically and look for ways to create value for their customers.
- Results include principles such as Deliver Value to the Customer, Achieve Operational Excellence, and Leading with Humility. These are focused on achieving measurable results and continuously improving the organization’s performance.
The Shingo Model is a powerful methodology for achieving operational excellence because it provides organizations with a set of principles and tools that can be used to create a culture of continuous improvement.
Lean Manufacturing
Lean manufacturing is an operational excellence methodology that aims to eliminate waste and maximize efficiency in production processes. It was developed by Toyota in the 1950s as part of the Toyota Production System (TPS) and has since been adopted by many other organizations around the world.
At its core, lean manufacturing is based on five principles: value, value stream mapping, flow, pull, and perfection. These principles are designed to help organizations identify and eliminate waste in their production processes, while also improving quality and reducing costs.
- Value: This refers to the creation of value for the customer and emphasizes the importance of understanding customer needs and preferences in order to create products and services that are truly valuable to them.
- Value stream mapping: This involves mapping out the entire production process from start to finish to help organizations identify areas of waste and inefficiency in their business processes.
- Flow: The smooth and continuous movement of materials and information through the production process. This aims to reduce bottlenecks and other obstacles that can slow down production and create waste.
- Pull: This is about producing goods only when they are needed to help organizations avoid overproduction and reduce the need for inventory.
- Perfection: The constant striving for continuous improvement and eliminating waste.
By identifying and eliminating waste in production processes, organizations can improve efficiency, reduce costs, and improve the quality of their product. This can lead to higher customer satisfaction, increased profitability, and a stronger competitive position in the market.
Six Sigma
First developed by Motorola in the 1980s, Six Sigma is a data-driven operational excellence methodology that aims to improve the quality and efficiency of processes in an organization.
The goal of Six Sigma is to reduce defects and variability in processes so that they operate at a level of 3.4 defects per million opportunities (DPMO) or better. This is achieved through a rigorous process of measurement, analysis, and improvement.
At its core, Six Sigma is based on a five-step process known as DMAIC, which stands for Define, Measure, Analyze, Improve, and Control:
- Define: defining the problem and setting goals for improvement to ensure that the organization is focused on the right issues and has a clear understanding of what needs to be improved
- Measure: collecting data on the process in question and analyzing it to identify areas of inefficiency understand the current state of the process, and determine what needs to be improved
- Analyze: using statistical tools to analyze data and identify the root causes of defects and variability in an effort to understand the underlying causes of problems and develop effective solutions
- Improve: developing and implementing solutions to address the root causes of defects and variability and achieve the goals set in the Define step
- Control: monitoring the process to ensure that the improvements are sustained over time
By reducing defects and variability in processes, organizations can Improve Work Performance, reduce costs, and increase customer satisfaction.
Kaizen
Kaizen is a Japanese word that means “change for the better” or “continuous improvement.” It is an operational excellence methodology that focuses on improving processes and systems by making small, incremental changes over time. The goal of Kaizen is to achieve sustainable improvements in quality, efficiency, and productivity.
Kaizen is based on the idea that every process can be improved, no matter how efficient it may seem to be. The methodology involves a systematic approach to identifying and eliminating waste, reducing variability, and improving quality. It is often used in manufacturing but can be applied to any process or system.
The Kaizen process involves a series of steps that are repeated continuously over time:
- Identify the area or process that needs improvement by looking at the process from a customer’s perspective, or analyzing the flow of materials, information, or people
- Measure the current state of the process by collecting data on the time it takes to complete each step, the number of defects or errors, or the amount of waste produced
- Analyze the data and identify the root causes of any problems or inefficiencies by using tools like flowcharts, fishbone diagrams, or statistical process control charts
- Develop and implement solutions by making small changes to the process, such as rearranging workstations, changing procedures, or introducing new tools or technology
- Monitor the process and measure results by collecting data on the time it takes to complete each step, the number of defects or errors, or the amount of waste produced
By focusing on continuous improvement with Kaizen, organizations can achieve sustainable improvements in quality, efficiency, and productivity.
Why Does Operational Excellence Matter?
Striving for operational excellence impacts almost every industry, including manufacturing, healthcare, technology, construction, etc. This is because it focuses on improving processes and systems.
So, what are the benefits of operational excellence, and how can you achieve them?
Let’s say a company’s first step to achieving operational excellence is transforming itself into a lean operations management organization.
Which of the following attributes is not for lean operations?
- Overproduction of products
- Frequent employee downtime
- Consistent inventory excess
- All of the above
So, which of the following attributes is not for lean operations? The answer: D. All of the above.
With the lean management method, companies benefit from waste elimination, operating expense reduction, and profit growth.
There are plenty of other benefits that impact the organization outside of operational metric improvement, including:
- Improved teamwork and collaboration
- A more empowered and productive workforce
- Better value to the customer and enhanced interactions and service
- Better and more open communication between organizational levels
How to Achieve Operational Excellence Through Communication?
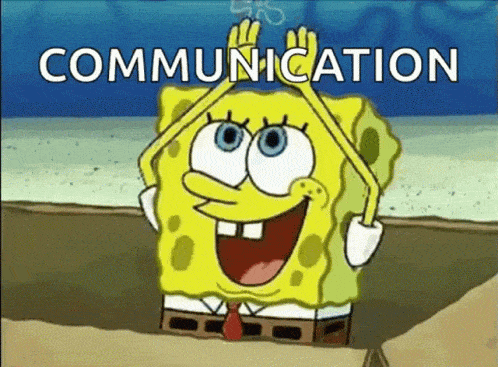
So, now that you have your operational excellence program in place — including your methodology and overarching goals – what next? How do you put the plan to work, and more importantly, how do you ensure sustainable progress?
Start by communicating with your employees and empowering them to find ways to be more efficient in their day-to-day tasks.
Get started with these five open employee communication tips:
- Communicate a clear business strategy. This helps employees understand how operational excellence supports overall business objectives and establishes an improved flow of value
- Share goals and KPIs. This allows employees to be crystal clear on what they are working to achieve
- Use communication tools that reach your workforce. Use mobile communication tools like Beekeeper that give instant access to information
- Provide training opportunities. Help employees take operational excellence into their own hands with leadership, process, and problem-solving education
- Be open to feedback. Frontline employees are usually the first to know when something can be done better to save time and money
Pro tip: Using Beekeeper surveys and 1:1 or group chats are an easy and quick way to gather frontline employee feedback.
A solid operational excellence strategy and execution plan are great to have, but it’s your workforce that brings the program to life.
You can extend the lifetime of your program by ensuring employees are:
- Communicated with openly
- Empowered to make their own decisions and provide feedback
- Trained to spot operational gaps in need of continuous improvement
Operational Excellence Examples
Operational excellence examples can be found across any industry you look to.
Below are some examples of how companies apply operational excellence to their business models to stay competitive.
Chevron
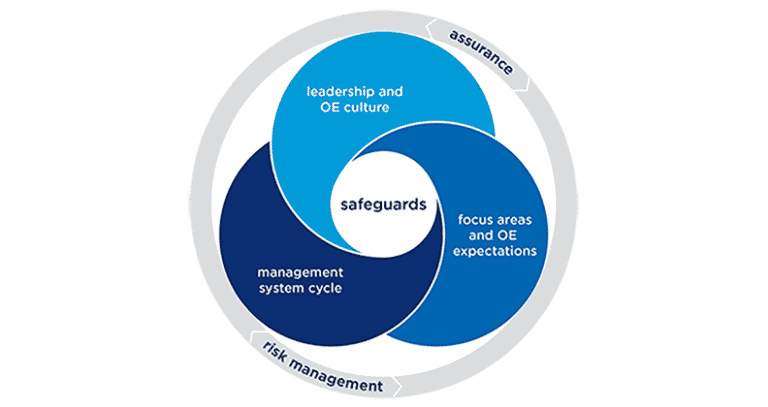
Chevron has a long history of putting an operational excellence culture at the forefront of its organization.
Its Operational Excellence Management System (OEMS), which launched in 2004, outlines a clear set of operational excellence objectives and focus areas. Employees are expected to help manage risks and maintain the safeguards in place that mitigate those risks.
According to Chevron’s CEO Mike Wirth, OEMS is what sets them apart from their competition: “OE is a competitive advantage in hiring and retaining the best workforce, and vital to building trust with communities and governments.”
IRP Meat and Seafood Co.
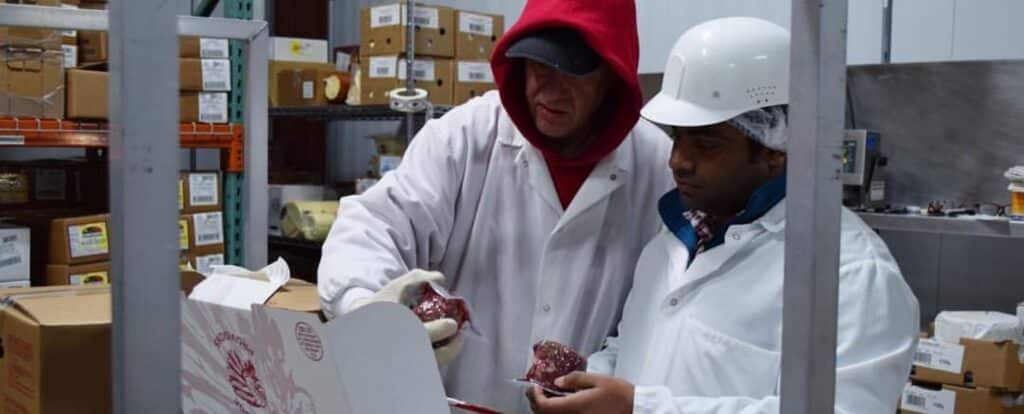
IRP Meat and Seafood Co. took its operational efficiency to the next level by transforming its frontline operations.
As a business whose customers frequently place “just in time” orders, IRP needed a better way for employees to communicate about customer orders.
Since adopting Beekeeper, operations improved by:
- Creating a streamlined workflow
- Reducing waste due to order changes
- Improving on-time deliveries for customers who rely on quick turnarounds
Which Industries Can Benefit from Operational Excellence
Because operational excellence focuses on process, many industries can stand to benefit from a well-thought-out program. However, different industries will look to improve different processes.
Industries that benefit from operational excellence are:
Manufacturing
The manufacturing industry is no stranger to operational excellence initiatives. As the Fourth Industrial Revolution takes hold, factories are under pressure to enhance productivity, decrease downtime, and cut out waste where they can.
Construction
Similar to Chevron, construction focuses heavily on employee health and safety as a measure of operational excellence success.
For example, Holcim Switzerland & Italy adopted the Beekeeper employee communication app to enhance operational health and safety communications that could be reached across their distributed workforce.
Healthcare
Like many industries, the healthcare industry is always looking for ways to cut costs while continuing to deliver exceptional patient care.
According to McKinsey, acute-care facilities are focusing on lean operations, clinical standardization, and supply utilization to unlock savings and achieve clinical operations excellence.
Operational Excellence Best Practices and Strategies
Achieving operational excellence is no simple matter. It takes a long time to plan your strategy.
When you’re ready to put your operational excellence plan into place, consider these five operations best practices.
1. Choose a Methodology That Matches Your Strategy
It’s best to start your operational excellence journey with a method that helps you achieve your goals as efficiently as possible.
The methodology you select, such as Lean Management, Six Sigma, and Kaizen methods, will be based on your focus area.
For example, if you’re looking to cut waste in your factory, you might go with Lean Management. If you’re looking to enhance the customer experience, you might consider Six Sigma.
Either way, start with a solid foundation by knowing exactly what it is you’d like to address and selecting the method that will help you get there.
2. Define Your Goals
Then, outline what it is you want to achieve – both with broad goals and specific KPIs that will measure your success.
For example, if you’d like to enhance the customer experience with a more knowledgeable workforce, set a goal for the amount of training employees should go through to understand the products and services better.
3. Get Employees Onboard As Soon As Possible
Don’t forget, your employees are the ones that will put your strategy to work to achieve operational excellence. Bringing them into the conversation as soon as possible is an important step.
To start, consider including employees that are the most impacted by any of the changes in the strategy process. Those employees can give you real-time insight into the problems the company is facing and why. They can also share their own ideas of how to address certain problems in the operational excellence program.
4. Communicate, Communicate, Communicate
As with any organizational change, communication is key to achieving operational excellence.
First, make sure to communicate the essential aspects of the program, such as the mission, goals, and KPIs, to those impacted.That way they have the full view of what your organization is trying to achieve. Then, provide an open feedback channel so employees, managers, and leaders can stay in close contact throughout the process.
5. Remember Operational Excellence Is Continuous
Unlike other corporate initiatives, operational excellence doesn’t stop once it’s achieved. It requires constant communication, continuous improvements, and workforce engagement to sustain growth and keep your company ahead of the competitive curve.
Frequently Asked Questions About Operational Excellence
What is the difference between operational excellence and operational efficiency?
Operational excellence is focused on consistently delivering value to customers through continuous improvement. It means optimizing every aspect of the company’s operations to eliminate waste, reduce costs and increase productivity. Operational efficiency refers to the ability of a company to use its resources effectively to achieve its desired outcomes. Operational excellence is more focused on delivering value to customers, while operational efficiency is more focused on resource optimization.
How can operational excellence benefit an organization?
Operational excellence can lead to:
- Increased customer satisfaction
- Positive customer feedback and repeat business
- Increased revenue
- Cost savings
- Better employee engagement
- Higher levels of employee satisfaction and retention
- Better risk management
- Sustainable growth
What are the common obstacles to achieving operational excellence?
Common obstacles include:
- Resistance to change from employees and leadership
- Lack of clear goals and metrics
- Inadequate training and communication
- Siloed departments and poor collaboration
- Not enough investment in technology
How can companies sustain operational excellence in the long term?
Sustaining operational excellence in the long term requires a commitment to ongoing training and development, a culture of innovation and experimentation, and a willingness to embrace change. Organizations must also prioritize cross-team collaboration and communication to identify and address issues quickly and effectively. Measuring and tracking progress against key performance indicators ensures that teams are meeting goals and continually improving.
What role does employee engagement play in operational excellence?
Employee engagement is essential to achieving operational excellence. Engaged employees are more motivated, productive, and committed to their work, leading to better business outcomes. When employees are engaged, they are more likely to take ownership of their work, identify areas for improvement, and actively contribute to the success of the organization. Organizations that prioritize employee engagement also typically have lower turnover rates and higher levels of customer satisfaction.
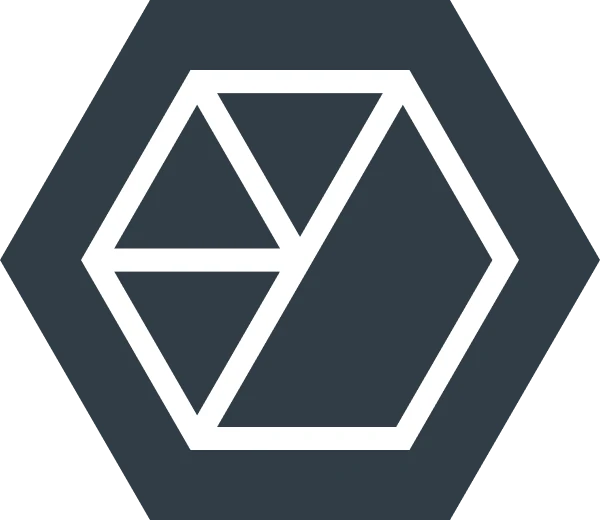
About the author
Beekeeper
We make frontline lives easier, work safer, and teams more connected so businesses can reach new heights. At Beekeeper, we’re dedicated to making frontline lives easier by connecting workers with the tools, support, and information they need to feel valued, do their best work, and drive the business forward.